U.S. Federal government-funded investments backed by billions of dollars are driving industrial development in certain areas of the country – and there are some massive buildings under construction. Consider Taiwan Semiconductor Manufacturing Co.’s (TSMC’s) chip fabrication plant in Greater Phoenix. Estimated at $40 billion, it is receiving funding from the CHIPS Act and is one of the largest construction sites in North America.
Suppliers to TSMC are also fueling demand for industrial buildings nearby. Developers are responding, including Opus. Soon we will complete Deer Valley 30, a three-building speculative industrial development near TSMC.
And this is only the beginning.
Large sums of money remain in bank accounts for government-funded programs like the CHIPS Act, the Infrastructure Investment and Jobs Act, and the Inflation Reduction Act. In fact, according to the public policy research organization Brookings, most of the $1.25 trillion in infrastructure spending approved by Congress and signed into law by President Biden was still available in early 2023.
In addition to those government investments, the onshoring trend is also driving demand for new industrial buildings. Exasperated by the pandemic, many businesses are choosing to “onshore” and move manufacturing back to the U.S. due to rising offshore labor costs, supply chain resilience, quality control and transportation costs, to name a few.
Government investments and onshoring are pumping millions of dollars into the pipeline for industrial development. If you are a general contractor or subcontractor working directly on those larger projects, high demand and solid financial backing should enable healthy margins. Private construction companies like Opus who are building supportive facilities are also benefiting from the increased demand.
However, with opportunities come challenges.
Allocation of materials
Markets like Phoenix are incredibly busy. Available building materials are often allocated for large projects like TSMC, straining resources for private construction companies delivering smaller supportive projects.
Overall, building supply shortages have moderated somewhat nationwide and the supply chain is less fragile than a year ago. However, certain materials and equipment are still difficult to procure due to extreme demand – like electrical switchgear.
Most of our industrial projects at Opus require custom-configured electrical switchgear. Component parts are common, but equipment is tailored to each user, adding to the complexity. At the time of writing this article, the equipment is difficult, if not impossible, to procure in a timely manner.
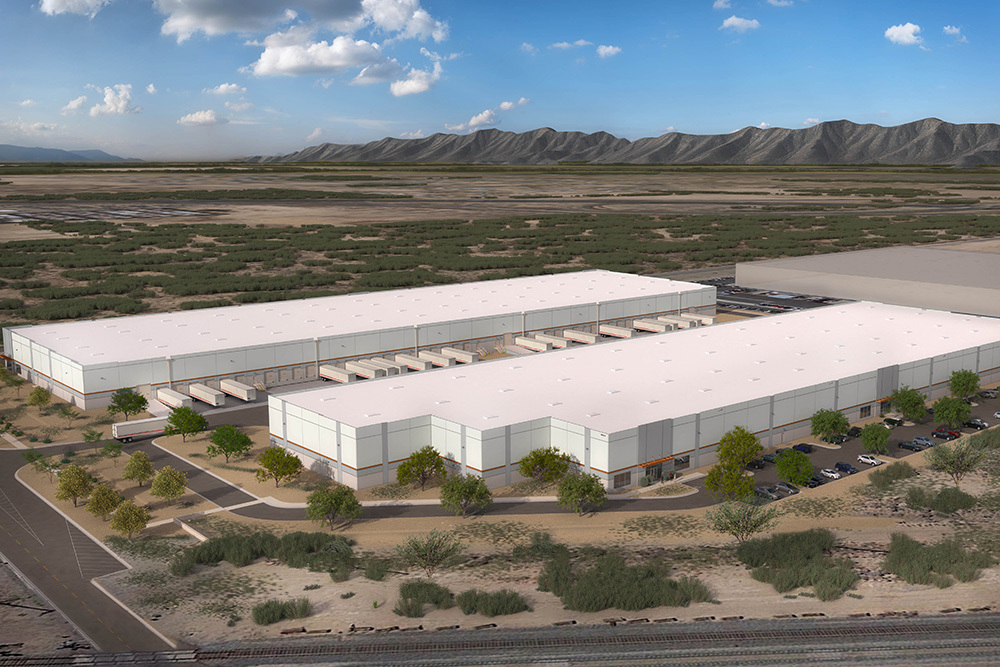
For instance, our electrical contractor ordered switchgear in Sept 2022 for Confluence Industrial Park, a 325,000-square foot, two-building speculative development in Casa Grande, Ariz. The lead time was initially estimated at 50 weeks, but it took 60 weeks – a three-month delay. This is not uncommon. Many contractors have similar stories. Prior to the pandemic, the normal lead time would have been about 26 weeks.
We have kept Confluence Industrial Park on schedule by changing the normal sequence of installation and related activities at the jobsite.
Pricing volatility
Before the pandemic, pricing for materials was trending up. Fast forward to today and especially given the massive projects underway, it can be difficult to pencil projects due to pricing. Pricing is volatile and poses inherent risk, as construction companies often lock down before signing contracts. Project lead times are long, so when predicting uncovered costs, it’s difficult to know how high prices will go.
We saw significant price spikes during the pandemic. With that behind us, the natural expectation would be for prices to bounce back down. As shown in this Federal Reserve producer price index image for non-residential construction, that isn’t happening. Historically speaking, construction prices tend to plateau and then continue rising, albeit at a gradual pace. Between 2022 and 2023, it was anything but gradual.
Construction usually follows the path of disinflation – a slowing down of the increases. Pricing could be flat or slightly down for a year or two, but without a considerable recession, we are likely near the new normal.
More-hands-on deck
The shortage of tradespeople was perhaps masked when the supply chain was severely constrained. If you couldn’t get materials, you didn’t need as many tradespeople.
That was temporary. The need for skilled tradespeople is rising to the top again. Awareness is heightened and demand is high, especially in markets with large government-funded projects. Even the most efficient subcontractors can have difficulties meeting all of their commitments.
At Opus we are design-build with in-house real estate development teams. This integrated model is highly efficient, but like everyone else, we need skilled boots on the ground and all hands-on deck.
Collectively an industry-wide effort is taking place across the country to promote careers in the trades. Led by construction firms and nonprofit organizations, a similar mantra is shared – with a career in the trades, you can make an excellent living without rolling up huge college debt.
And there’s a good case for that.
In 2022, the typical undergraduate student with loans graduated with nearly $25,000 in debt according to the U.S. Department of Education. The cost of both public and private four-year colleges has nearly tripled since 1980, per the College Board. Meanwhile federal support through Pell Grants for working families has decreased from covering nearly 80 percent of the cost of a four-year public college degree to approximately 30 percent. It’s tougher than ever to swing a college education – and that makes the trades more attractive.
In addition to national organizations like SkillsUSA, many regional and state-specific organizations provide hands-on training, apprenticeships, and job placement assistance. For example, Opus supports Construction Careers Foundation, a nonprofit organization in Minnesota working to increase diversity in the trades and fostering long-term construction careers. We also created an internship program that provides on-the-job training and mentoring for students interested in construction, architecture and design, and real estate development.
In construction, the majority of work requires human hands – no amount of AI can replace it and robots are a novelty at this point. That’s job security. Unless there are sweeping changes on the technology front, working in the trades will become more attractive because it's hard to replace.
Forward looking lens
There are reasons to be optimistic going into 2024 and beyond. The industry is acutely aware of the shortage of tradespeople. The issue is moving to the forefront once again and garnering a great deal of attention. Initiatives are underway to address it. There’s a lot of work to be done, but I am hopeful that in the coming years we will start to feel the effects.
We are also past the worst of the material shortages. The supply chain is expected to continue moderating, enabling the industry to return to a more normal mode of operation. Pricing will continue to cause pain, but that should moderate as well. As the cost of constructing buildings goes up, rents will go up too. And tenants will pass those costs on to their customers, and so on. As long as there’s demand for buildings, higher costs will get absorbed through the system.
About the Author
Tom Becker is President and CEO of Opus Design Build. He can be reached at Tom.Becker@opus-group.com.
Related Stories
| Jul 17, 2013
CBRE recognizes nation's best green research projects
A rating system for comparative tenant energy use and a detailed evaluation of Energy Star energy management strategies are among the green research projects to be honored by commercial real estate giant CBRE Group.
| Jul 2, 2013
LEED v4 gets green light, will launch this fall
The U.S. Green Building Council membership has voted to adopt LEED v4, the next update to the world’s premier green building rating system.
| Jul 1, 2013
Report: Global construction market to reach $15 trillion by 2025
A new report released today forecasts the volume of construction output will grow by more than 70% to $15 trillion worldwide by 2025.
| Jun 28, 2013
Building owners cite BIM/VDC as 'most exciting trend' in facilities management, says Mortenson report
A recent survey of more than 60 building owners and facility management professionals by Mortenson Construction shows that BIM/VDC is top of mind among owner professionals.
| Jun 17, 2013
DOE launches database on energy performance of 60,000 buildings
The Energy Department today launched a new Buildings Performance Database, the largest free, publicly available database of residential and commercial building energy performance information.
| Jun 12, 2013
5 building projects that put the 'team' in teamwork
The winners of the 2013 Building Team Awards show that great buildings cannot be built without the successful collaboration of the Building Team.
| Jun 5, 2013
USGBC: Free LEED certification for projects in new markets
In an effort to accelerate sustainable development around the world, the U.S. Green Building Council is offering free LEED certification to the first projects to certify in the 112 countries where LEED has yet to take root.
| Jun 3, 2013
Construction spending inches upward in April
The U.S. Census Bureau of the Department of Commerce announced today that construction spending during April 2013 was estimated at a seasonally adjusted annual rate of $860.8 billion, 0.4 percent above the revised March estimate of $857.7 billion.
| May 17, 2013
University labs double as K-12 learning environments
Increasingly, college and university research buildings are doing double duty as homes for K-12 STEM programs. Here’s how to create facilities that captivate budding scientists while keeping faculty happy.
| May 1, 2013
Data center construction remains healthy, but oversupply a concern
Facebook, Amazon, Microsoft, and Google are among the major tech companies investing heavily to build state-of-the-art data centers.