The construction and design industries are witnessing a significant shift towards energy-efficient spaces, driven by more stringent building energy codes, increased initiatives and legislation focused on reducing carbon in materials used for building projects and a growing public interest in environmental impact.
While energy efficiency and operational carbon are significant factors in environmentally conscious construction, it’s important to underscore the importance of embodied carbon emissions, which continue to gain traction as a major focus in today’s sustainable design landscape. Architects are increasingly opting for products with low embodied carbon, a term that refers to emissions caused by the manufacturing and installation of construction materials. When assessing the embodied carbon in building products, including glass, the industry standard metric is Global Warming Potential (GWP), measured in kilograms of equivalent carbon dioxide per metric ton (CO2-eq). GWP is used to evaluate the environmental impact of a product's life cycle.
Previously, there was no standard for “low embodied carbon” (LEC) building products; however, there is now. The U.S. Federal Government’s Federal Buy Clean Initiative was established to promote using and developing low-carbon, made-in-America construction materials. In establishing best practices for the U.S. building products industry, standards for LEC products were set by the U.S. General Services Administration (GSA) under the Inflation Reduction Act of 2022 and related guidance from the U.S. Environmental Protection Agency. By these standards, LEC products can fall into three different product categories according to embodied carbon content: Top 20%, Top 40%, and exceeds the industry average.
As the market shifts towards eco-friendly spaces that increase energy efficiency and lower carbon emissions that promote occupant health and well-being, the availability of high-performance architectural glass configurations that significantly boost thermal capabilities and reduce the building's carbon footprint is also on the rise.
Measuring Energy Performance
When assessing the energy efficiency of glass, the U-value, also known as the U-factor, stands out as one of the most critical performance indicators. This metric is a pivotal indicator of the insulating properties of the glass, or in simpler terms, it gauges the amount of heat flow or heat loss that occurs through the glass due to the temperature difference between the interior and exterior. U-values typically span from 0.1 to 1.0. The lower the U-value, the more efficient the insulation. The U-value of a window is determined by the number of British thermal units (Btus) that traverse each square foot of area per degree of temperature difference from one side of the window to the other.
Alongside U-value, R-value is another important metric in thermal performance. U-value is used to measure the performance assemblies of insulating glass units (IGUs), while R-value is used to measure the capabilities of most other parts of the building envelope, such as walls, floors, and roofs. These two values are mathematical reciprocals of each other. Lower U-values indicate better insulating performance, whereas higher R-values indicate better thermal resistance.
More Options than Ever to Enhance U-value
Thanks to the advent of low-emissivity (low-e) coatings and technologies for IGUs, architects now have diverse options to enhance U-values wherever enhanced thermal performance is needed. These cutting-edge choices can enhance thermal potential by two or even three times, leading to substantial annual energy savings and surpassing sustainable design objectives for reducing energy consumption and carbon emissions.
Along with traditional methods to improve U-values, such as using low-e coatings and dual- or triple-pane IGUs with argon gas or warm-edge spacers, new technologies like fourth-surface low-e coatings and vacuum insulating glass (VIG) are transforming the thermal capacity of buildings, offering exceptional improvements in durability and insulation without changing the visual characteristics of the IGU.
Fourth-Surface Low-e Coatings
Fourth-surface low-e coatings are designed to be used on the inside surface of an IGU, and when combined with solar control low-e glass on the second surface, they can significantly improve U-values while still allowing a high rate of visible light transmittance (VLT). These coatings effectively retain indoor temperatures by slowing heat transfer through the IGU. This can help reduce summer cooling costs and winter heating costs, resulting in up to a 20% improvement in the U-value compared to using solar control low-e glass alone on the second surface.
Vacuum Insulating Glass (VIG)
VIG is an innovative high-performance glass that utilizes vacuum technology and a low-e coating in an IGU to provide exceptional thermal capabilities comparable to traditional walls. VIG units typically can be used on their own to replace single-pane glass without replacing the framing system, or they can be used as a substitute for the interior lite in a dual-paned IGU, forming a hybrid IGU. VIG units with a low-e coating can have R-values up to R-20, offering thermal capabilities five times better than conventional insulating glass and up to 20 times better than monolithic glass. They can be incorporated into virtually any traditional glazing system, window frame or curtain wall application.
Advanced Technologies Substantially Improve Thermal Performance
Below is a chart of U-value comparisons for various glass configurations calculated using a baseline of a Dual-Pane Low-e 1” IGU Solarban® 70 (2) Clear + Clear with argon from Vitro Architectural Glass, with a U-value of 0.24. Based on these configurations, the overall thermal performance of a building can be improved by up to 79%. If expressed as R-values, the percentage of improvement would be even more substantial.
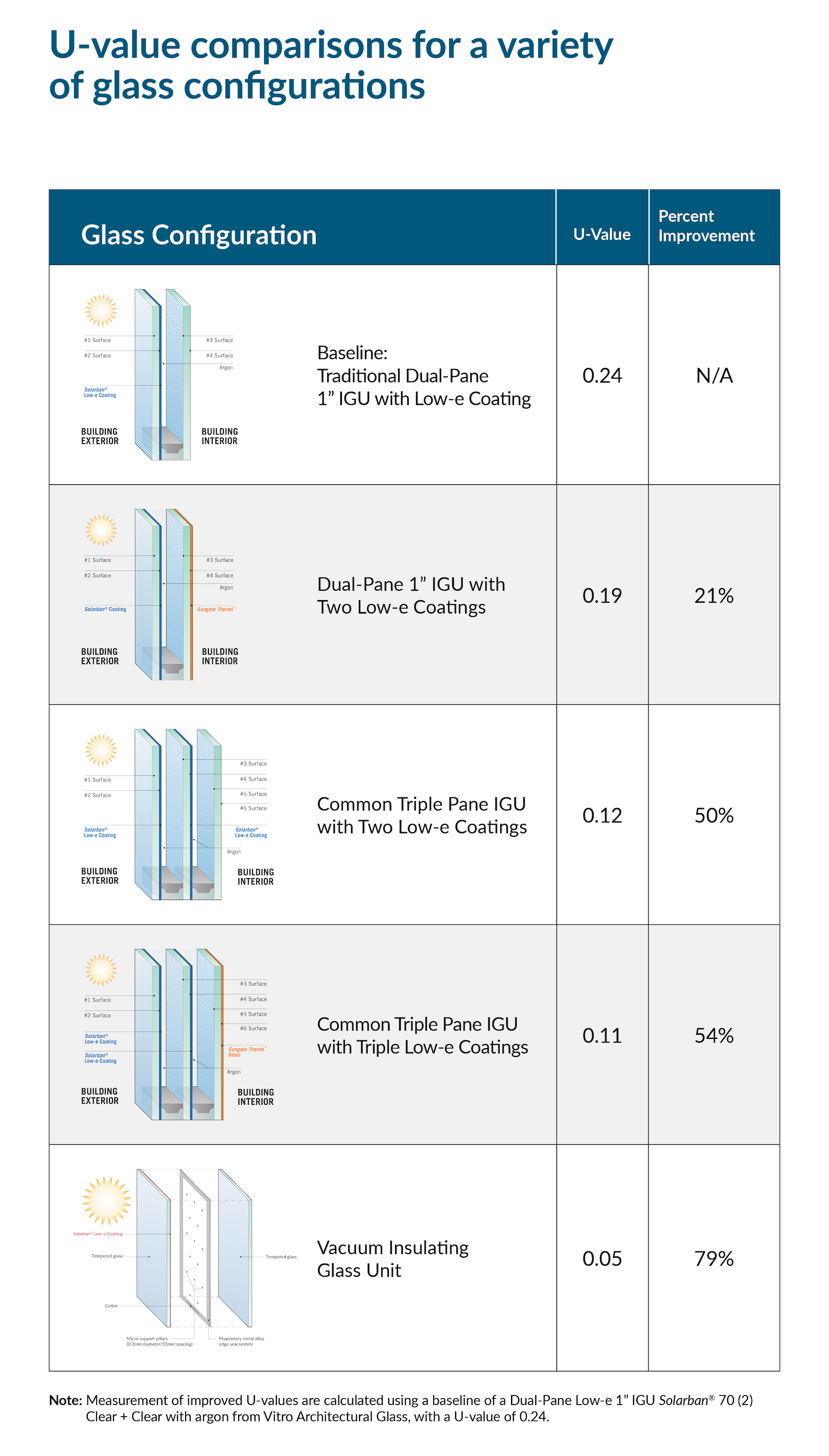
Building on the improvements that dual- and triple-pane IGUs have offered for decades, advancements in energy-efficient technologies, such as fourth-surface low-e coatings and VIG, represent the next generation of thermal glazings. These new high-performance IGUs significantly improve thermal insulation capabilities, energy savings and the overall sustainability of the building.
As building code standards demand more energy-efficient products in the future, U-value-optimized IGUs will play a major role in new construction or renovations as they ensure compliance with building energy codes, exceed sustainable design goals and leave a positive environmental impact.
About the Author
Emily Losego is the Director of Commercial Segment Innovation for Vitro Architectural Glass. She works with Vitro’s Marketing & Innovation Team to bring new glass product ideas from the drawing board to the production line. A former practicing architect, national architectural manager and magnetron sputter vacuum deposition (MSVD) product manager for Vitro, Losego is responsible for defining the vision for the architectural commercial market.
Related Stories
| Oct 14, 2014
Proven 6-step approach to treating historic windows
This course provides step-by-step prescriptive advice to architects, engineers, and contractors on when it makes sense to repair or rehabilitate existing windows, and when they should advise their building owner clients to consider replacement.
| Sep 25, 2014
Arup's Solarleaf façade system wins Zumtobel innovation award
The system uses the bio-chemical process of photosynthesis to absorb CO2 emissions, while cultivating microalgae to generate biomass and heat as renewable energy resources.
Sponsored | | Sep 15, 2014
Fire resistance of metal cladding is an asset in wildfire-prone areas
Construction projects in fire-prone areas need to take wildfire danger into account, and metal panels provide some fire-resistant qualities.
| Sep 5, 2014
Tyco SimplexGrinnell receives Internet of Things Innovator of the Year Award
The award recognizes the company for excellence in leveraging advanced Internet-connected technology to deliver smart eService fire alarm solutions that improve service delivery and provide significant value to customers.
| Aug 21, 2014
Firestone Building Products' Bristol facility chosen as Northeast business leader for energy efficiency
Firestone Building Products Company, LLC announced that its Bristol, Conn. manufacturing facility was recognized by the Northeast Energy Efficiency Partnerships (NEEP) as a 2014 Northeast Business Leader for Energy Efficiency.
| Aug 5, 2014
New bomb-proof concrete mixture used in One World Trade Center
The new concrete mix deforms instead of breaking, removing the threat of flying debris in an explosive attack.
| Aug 1, 2014
Johns Manville realigning Engineered Products into global business unit
New structure of Johns Manville Engineered Products unit expected to enhance customer experiences while strengthening innovation, agility, and manufacturing capabilities.
| Jul 17, 2014
A harmful trade-off many U.S. green buildings make
The Urban Green Council addresses a concern that many "green" buildings in the U.S. have: poor insulation.
| Jul 15, 2014
Trade groups form task force to further transparency and optimization of building product ingredients
The Harmonization Task Group will offer marketplace benefits including consistent messaging, simplification, elimination of redundancies, and creation of more accurate, faster and less costly assessments.
| Jul 10, 2014
Vetrotech Saint-Gobain first fire-rated glass ceramic fabricator to assess products' environmental footprint
Vetrotech is the first fire-rated glass company in the world to have made a comprehensive life cycle assessment of fire-rated glazing products.