BRONZE AWARD
University of California, Riverside Plant Growth Environments Facility, Riverside, Calif.
Project Information
Project size: 31,500 sf
Project cost: $21,993,111
Construction time: May 27, 2019 – November 23, 2020
Delivery method: Design-Build
Building Team
Submitting firm: DPR Construction
Owner: University of California, Riverside
Architect: Perkins and Will
Structural engineer: Coffman Engineers
Mechanical engineer: TK1SC
General contractor and Construction manager: DPR Construction
Judges’ comments:
“Amazing design and construction efforts can be very simple in concept. This project provides an elegant, detailed, collaborative solution that utilized all of the talents of the builder.”
“The raw and honest materials tie in well to the project’s agrarian roots. The GC’s ability to supplement/take over the work of a sub-tier contractor that went under reinforced its team commitment to the project.”
Essay from submitting firm:
Throughout its history, UC Riverside has been associated with the agricultural and natural sciences. Its main campus includes a district of greenhouses that were built in the 1960s. Nearly four decades later, the design-build team of DPR and Perkins and Will, along with subcontractor Stuppy Greenhouse, was responsible for creating a state-of-the-art research facility that puts science at UC Riverside on display.
The design team looked at this project as an opportunity to continue the tradition of campus architecture and create a design that balances being a contextual building with programmatic and campus goals. These include a focus on sustainability, enhancing the greenways of the campus, and fostering the collaborative culture of the campus and program.

Goals and Objectives
The two-story facility on one acre replaced older greenhouses made from wooden slats. It was constructed with concrete walls on the first floor and glass-encased greenhouses elevated above. The design used the concrete façade as the enclosure, structure, shading, and thermal mass, which links the building systems to eliminate the need for insulation, relying purely on the concrete’s thermal characteristics.
Individual growth chambers on the first-floor house plants, pathogens, and insects in separate, controlled environments. Each greenhouse module on the top floor incorporates wireless technology to adjust its own temperature, humidity, and lighting, allowing an array of plants to grow there. The facility also includes laboratory and workspaces and is the first in a series of plant growth spaces planned to replace aging greenhouses at UC-Riverside.
The raw construction materials used on the Plant Growth Environments Facility were selected to provide an unvarnished look in honor of the simplicity and beauty of the landscape.

BUILDING TEAM COLLABORATION
From the beginning of the project, the design-build team analyzed design, programming, and construction simultaneously. Concepts and solutions were assessed for design merit, functionality, constructability, and coordination. That team brought vetted ideas to design and planning meetings, through which it suggested a new planning strategy that resulted in a more than 15 percent increase of research space within the greenhouses, with no increase in cost or gross square footage.
Filling an unexpected labor gap
However, the project team faced a significant challenge when a sub-tier contractor that was slated to assist Kansas City-based design-build subcontractor Stuppy Greenhouse with the specialized greenhouse construction process went out of business. The team had to devise a way to get the project back on track and ensure it would be completed as planned and to the satisfaction of the owner.
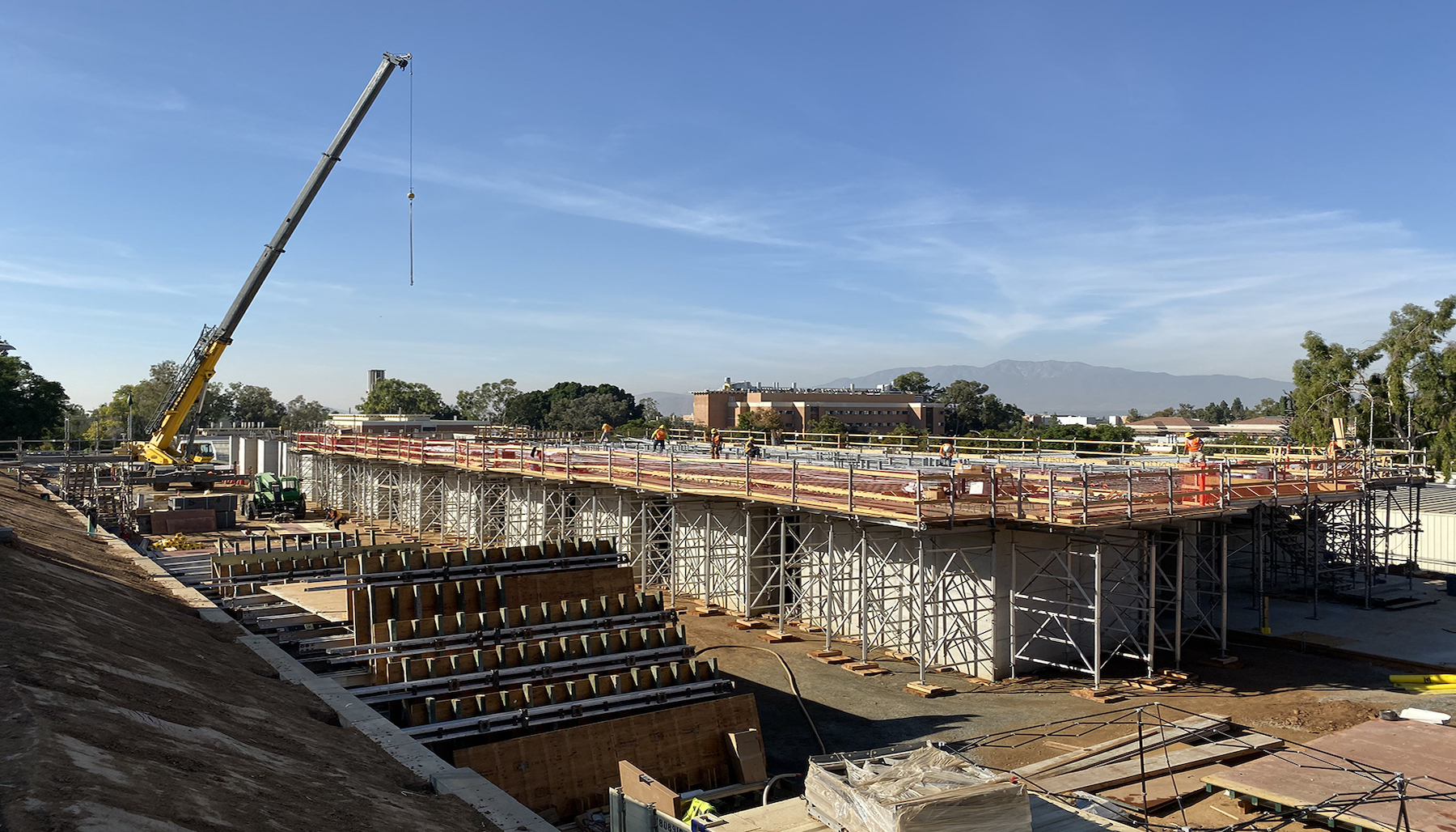
Facing the need for labor and crews to help erect the specialized greenhouse structure, DPR brought on its own self-perform carpenters to supplement Stuppy’s workforce, ultimately delivering about 10 percent of that subcontract volume. DPR’s self-perform concrete crews were responsible for delivering approximately 15 percent of the total project contract volume.
DPR superintendents were fully integrated into the subcontractor’s crews; likewise, DPR integrated Stuppy’s management team into the onsite project management team, according to project manager Paul Brown. “We took a ‘lean in’ approach to figure out a different way to get this done,” he said. “We brought everyone together to figure out a solution that would best serve the project.”
At the time work was to begin on framing the greenhouse, DPR’s concrete crew was on-site, completing the cast-in-place structure that would serve as the first-floor foundation for the glass building.
Managed material handling
The site was tight, with only one point of access and limited space between the site wall and finished concrete structure to receive and offload material. Because of the high risk of loading and offloading materials and the lack of a certified forklift driver on the part of the greenhouse vendor, DPR’s self-perform group pivoted to take on the scope of managing the hundreds of thousands of intricate pieces making up the state-of-the-art research facility.
“Given the small site and elevated work platform, material management was no small task,” said Damon Hole, who served as superintendent on the project.
Related Stories
Architects | Jan 18, 2016
EHDD’s Monterey Bay Aquarium wins AIA Twenty-five Year Award
The aquarium set new technical standards for the building type, which still influence today, such as the flow-through seawater-based heat pump system, naturalistic exhibitions, and corrosion protection.
Building Team Awards | Apr 10, 2015
14 projects that push AEC teaming to the limits
From Lean construction to tri-party IPD to advanced BIM/VDC coordination, these 14 Building Teams demonstrate the power of collaboration in delivering award-winning buildings. These are the 2015 Building Team Award winners.
Building Team Awards | Apr 10, 2015
Prefab saves the day for Denver hospital
Mortenson Construction and its partners completed the 831,000-sf, $623 million Saint Joseph Hospital well before the January 1, 2015, deadline, thanks largely to their extensive use of offsite prefabrication.
Building Team Awards | Apr 10, 2015
Anaheim’s soaring intermodal hub
Anaheim's Regional Transportations Intermodal Center is the largest ETFE project in North America.
Building Team Awards | Apr 10, 2015
Virtual collaboration helps complete a hospital in 24 months
PinnacleHealth needed a new hospital STAT! This team delivered it in two years, start to finish.
Building Team Awards | Apr 10, 2015
New arts venue reinvigorates Virginia Tech's campus
The STV-led Building Team creates a world-class performance and arts venue with learning and entrepreneurial dimensions.
Building Team Awards | Apr 9, 2015
Multifaced fitness center becomes campus landmark
A sloped running track and open-concept design put this Building Team to the test.
Building Team Awards | Apr 9, 2015
Nation's first LEED-certified bus depot
A bus garage in Harlem shows that even the most mundane of facilities can strut its environmentally sensitive stuff.
Building Team Awards | Apr 9, 2015
Setting the bar for port-of-entry design
Whenever you eat a tomato from Mexico, there’s a one-in-three chance it came through this LEED Gold gateway.
Building Team Awards | Apr 9, 2015
Big D’s billion-dollar baby: New Parkland Hospital Tops the Chart | BD+C
Dallas’s new $1.27 billion public hospital preserves an important civic anchor, Texas-style.