Months ago we heard news of the “nation’s first carbon-positive hotel”—a 13-floor, 130-000-sf cement tower with a triangular layout and eye-shaped windows. Populus, designed by Studio Gang and developed by Urban Villages, broke ground in Denver, Colo., last year with plans to be operational by summer 2024. What makes Populus a carbon-positive project is a collection of variables, from minimizing waste to using fewer finish materials. But there’s one huge driver behind the green initiative: sustainable concrete.
ECOPact is an optimized, low-carbon concrete made from large amounts of supplementary cementitious materials (SCM). With lower embodied carbon content compared to conventional concrete, ECOPact aims to be an attractive alternative for sustainability-driven engineers.
Sustainable concrete: ECOPact
Designed by Holcim, a sustainable building materials supplier, ECOPact offers a low-carbon alternative that not only meets, but exceeds the properties of standard (CEM I) concrete. This allows the material to be used in all traditional applications: structural components like foundations, columns and beams; to walls, driveways, bridges, and more.
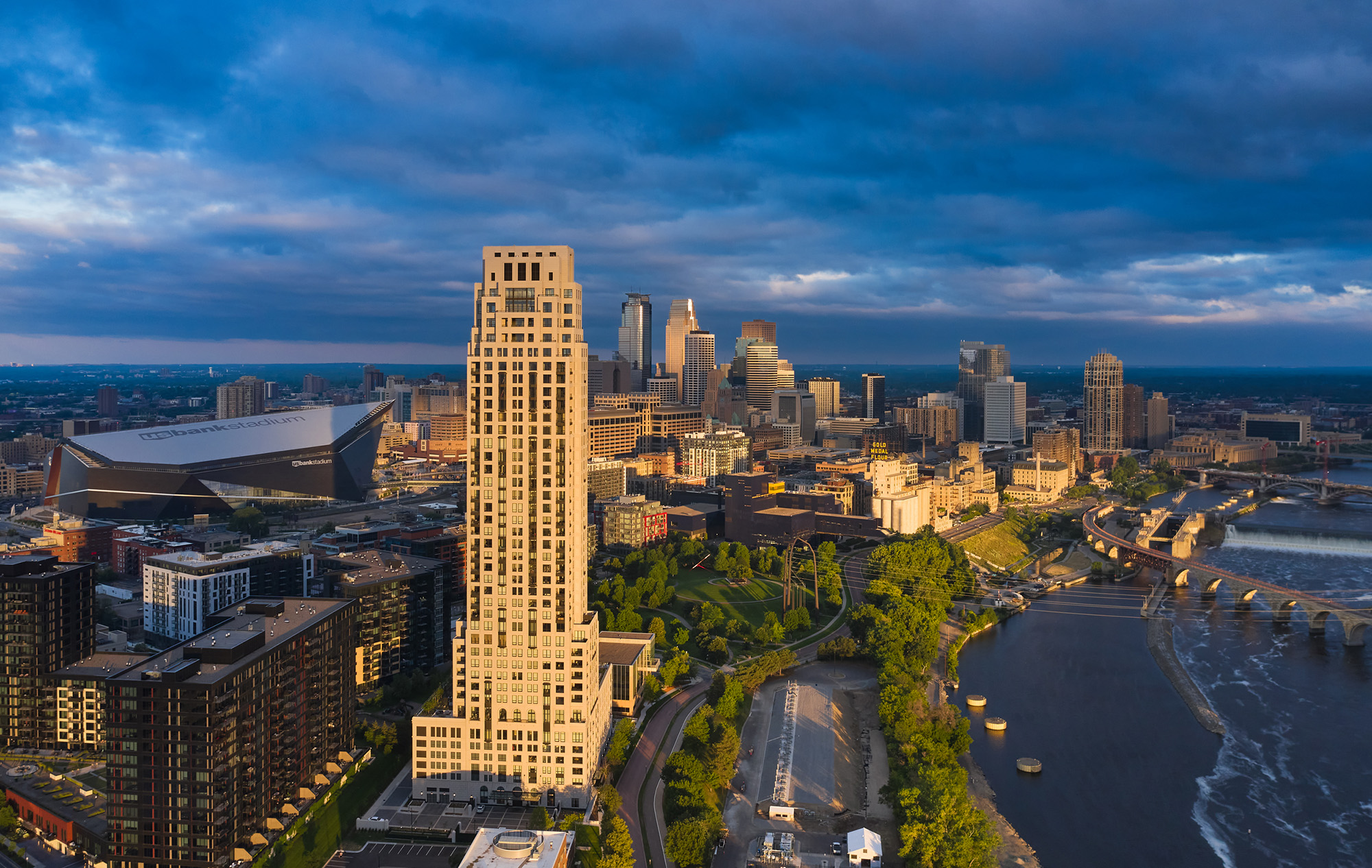
ECOPact Tiers
Rather than having a one-size-fits-all product, Holcim delivers ECOPact in a three-tiered system:
- ECOPact (30–50% reduction in carbon emissions)
- ECOPact Prime (50–70% reduction)
- ECOPACT Max (70–90% reduction)
Each tier can be enhanced with the addition of recycled concrete aggregates ECOPact+ range, according to the company. Kevin Peart, Senior Vice President and General Manager of the Mountain Region, Holcim, believes that Holcim has become “one of the first movers in the concrete industry.”
For the Populus hotel, this sustainable concrete was integral to the design process. The project’s utilization of ECOPact accounts for 65% of the total cubic yards of concrete poured, with an anticipated reduction of 765 tons in the concrete's embodied carbon compared to traditional concrete.

A similar story is told at 55 H Street, a Georgetown University residence hall (above). The project team had a specific challenge: they needed a concrete blend capable of attaining a 28-day design strength of 5,000 psi, while also achieving a high-early strength of 3,000 psi within a span of two to three days. ECOPact delivered, and 55 H Street became “one of the most sustainable buildings in D.C.,” says Zachary Lovett, Project Pursuit Manager, Holcim.
As the built environment continues to find ways to reduce its impact on the planet, innovative materials like ECOPact may help drive the change that architects, engineers, and contractors desire.
Related Stories
| Sep 24, 2012
Reed Construction completes Lafarge headquarters in Chicago
Reed Construction was contracted to complete the full third floor build-out which included the construction of new open area work space, private offices, four conference rooms with videoconferencing capabilities and an executive conference boardroom.
| Aug 30, 2012
Holcim (US) announces new Deputy Chief Executive Officer
Ruiz began his career with the Holcim Group in 1986 as electrical supervisor with Holcim Apasco, Mexico, later becoming plant manager.
| Jun 6, 2012
SOM urges Chicago tenants to partner with landlords to cut energy use
Tenants can exceed building energy challenge targets recently announced by Mayor Emanuel.
| Jun 1, 2012
New BD+C University Course on Insulated Metal Panels available
By completing this course, you earn 1.0 HSW/SD AIA Learning Units.
| Jun 1, 2012
AIA 2030 Commitment Program reports new results
The full report contains participating firm demographics, energy reduction initiatives undertaken by firms, anecdotal accounts, and lessons learned.
| Jun 1, 2012
New York City Department of Buildings approves 3D BIM site safety plans
3D BIM site safety plans enable building inspectors to take virtual tours of construction projects and review them in real-time on site.
| May 30, 2012
Construction milestone reached for $1B expansion of San Diego International Airport
Components of the $9-million structural concrete construction phase included a 700-foot-long, below-grade baggage-handling tunnel; metal decks covered in poured-in-place concrete; slab-on-grade for the new terminal; and 10 exterior architectural columns––each 56-feet tall and erected at a 14-degree angle.
| May 29, 2012
Reconstruction Awards Entry Information
Download a PDF of the Entry Information at the bottom of this page.
| May 24, 2012
2012 Reconstruction Awards Entry Form
Download a PDF of the Entry Form at the bottom of this page.