Researchers at ETH Zurich, a university in Switzerland, have developed a new robotic additive manufacturing method to help make the construction industry more sustainable. Unlike concrete 3D printing, the process does not require cement.
According to a press statement from ETH Zurich, the robotic printing process, called impact printing, uses cheap, abundant, and low-carbon earth-based materials such as clay or excavated earth. Currently, the robotic additive manufacturing method uses a mix of excavated materials, silt, and clay. Most of the custom material is common waste product sourced locally from Eberhard Unternehmungen, a Swiss construction company. In the future, the process could use other materials.
With ETH Zurich’s method, a robot deposits material from above, gradually building a wall. On impact, the pieces of material bond together, with minimal additives. Whereas concrete 3D printing creates layers, ETH Zurich’s method extrudes and drops the material one bit at a time at velocities of up to 10 meters per second. The fast speed allows the material to bond quickly.
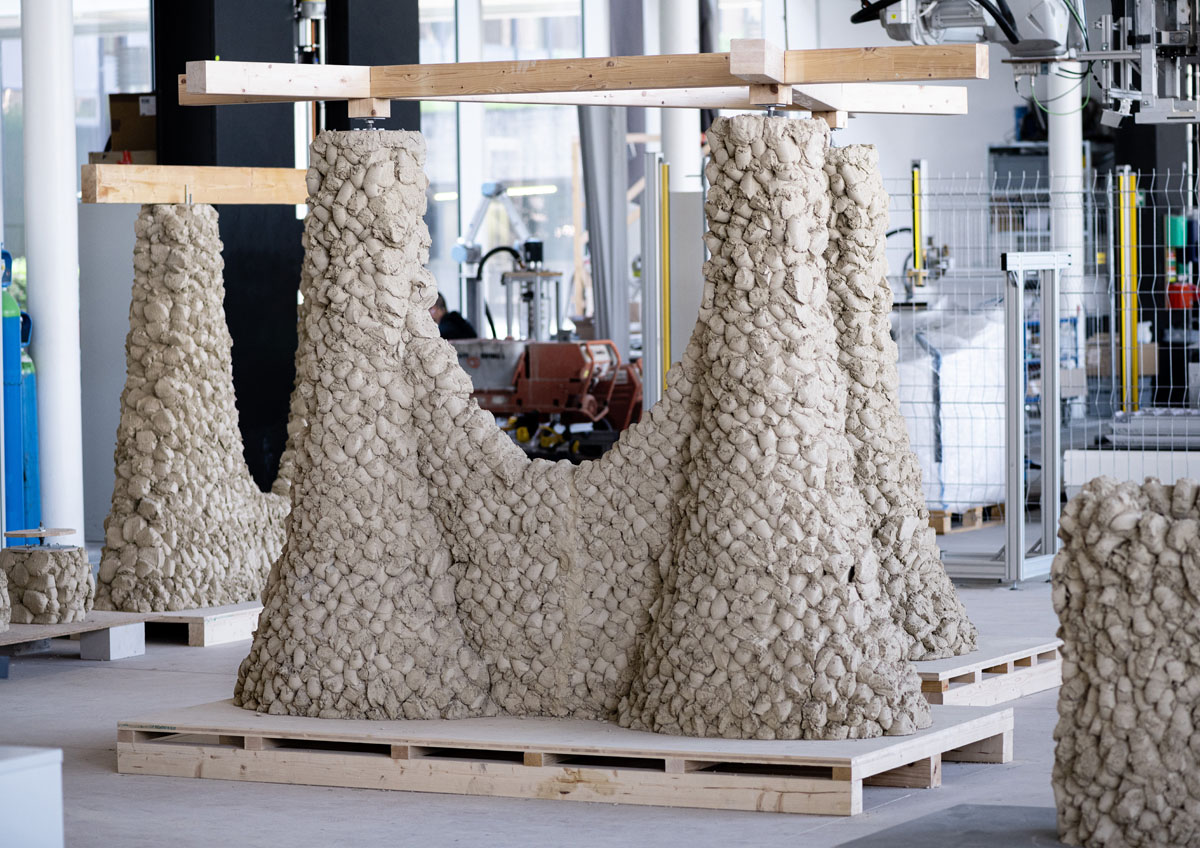
ETH Zurich’s process can build full-scale, freeform structures, including one- or two-story walls and columns. The printing tool has been used to build structures as tall as almost 10 feet. The process results in walls with a bumpy texture, but robotic surface finishing methods can achieve a smoother finish.
The custom printing tool can be integrated with multiple robotic platforms. As a result, the tool can build walls in both offsite facilities and onsite construction projects. At ETH Zurich’s Robotic Fabrication Laboratory, the tool has been integrated with a high-payload gantry system. The hardware can be mounted on an autonomous legged excavator to build walls on sites with variable terrain.
ETH Zurich says it aims to increase the cost competitiveness of sustainable building materials through efficient and automated production.
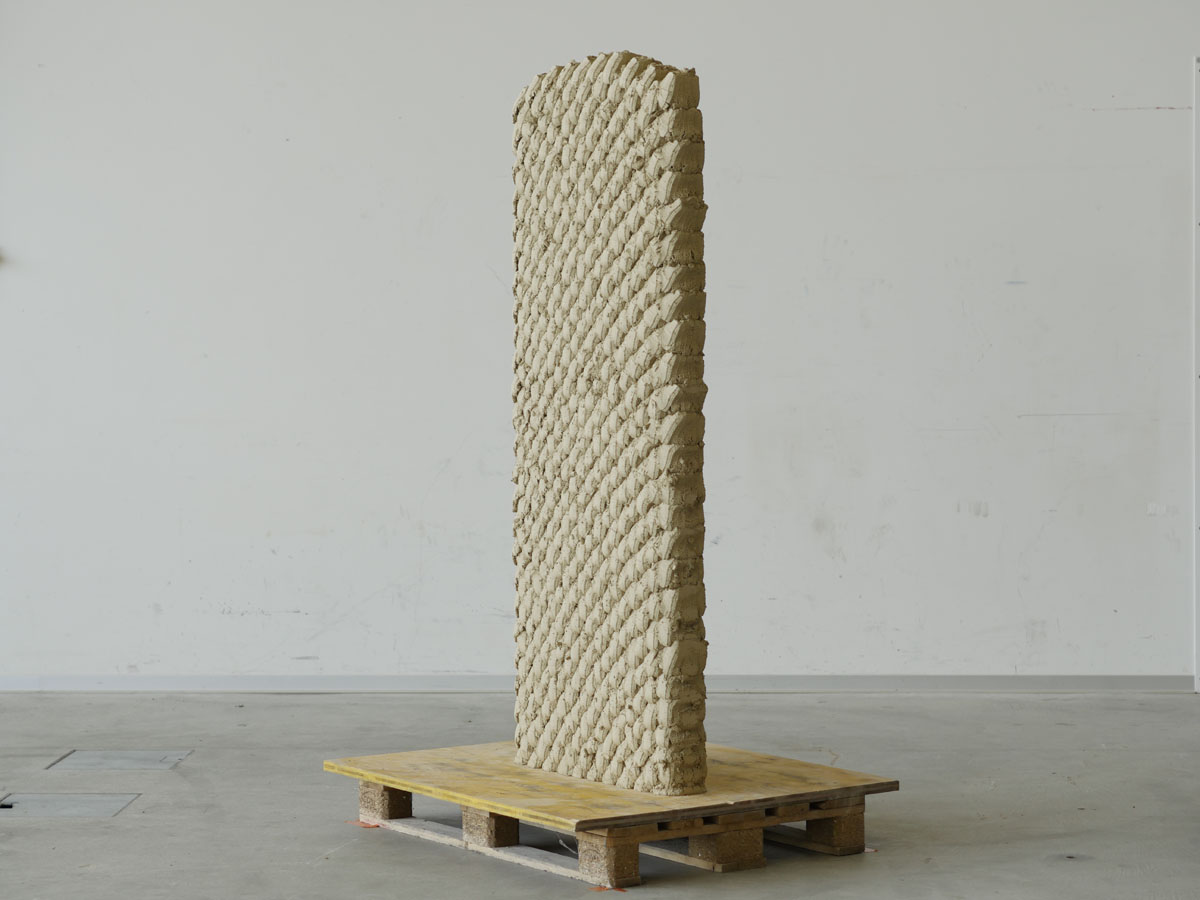
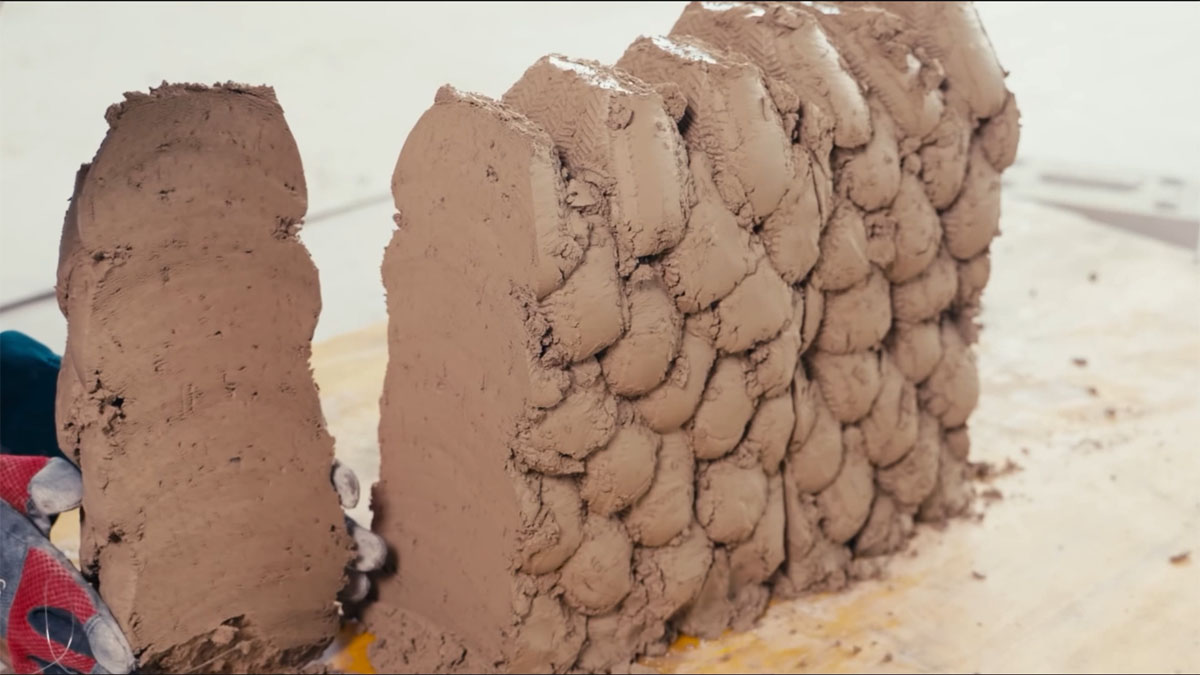
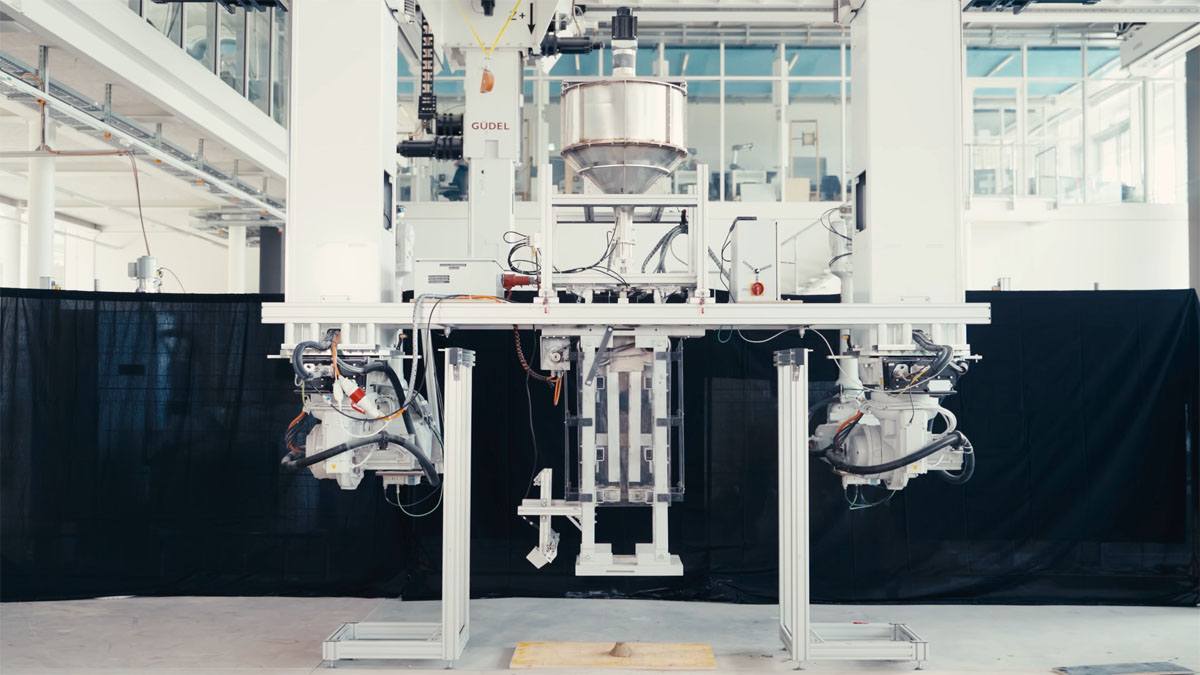
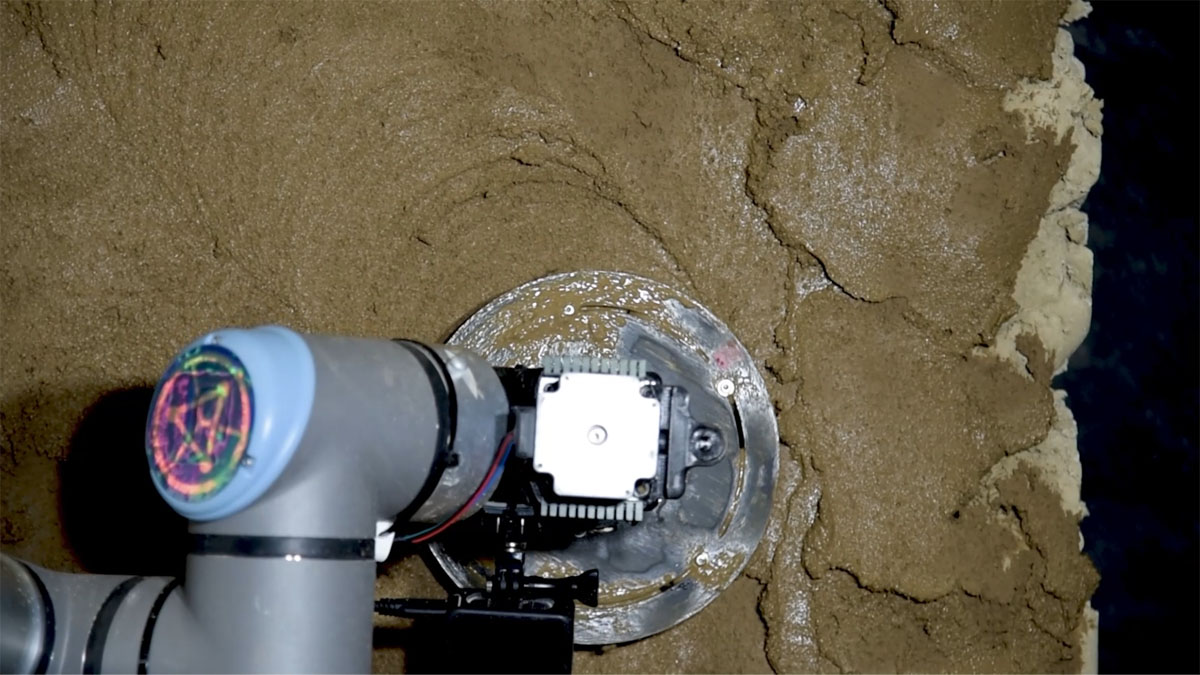
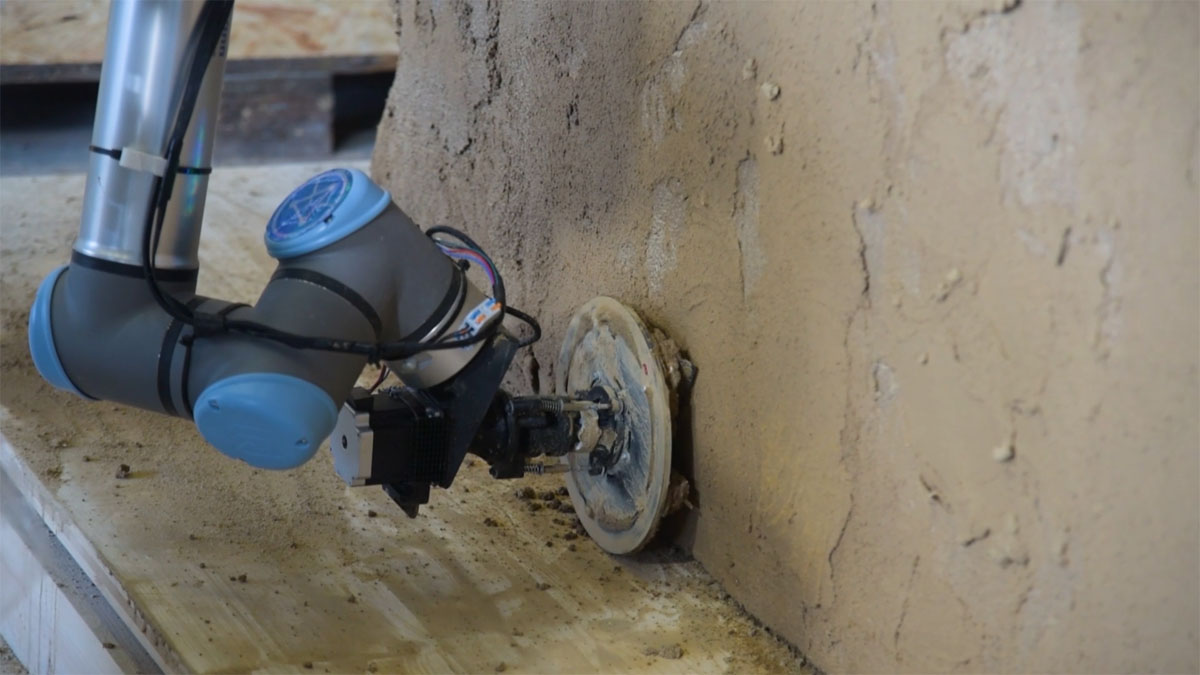
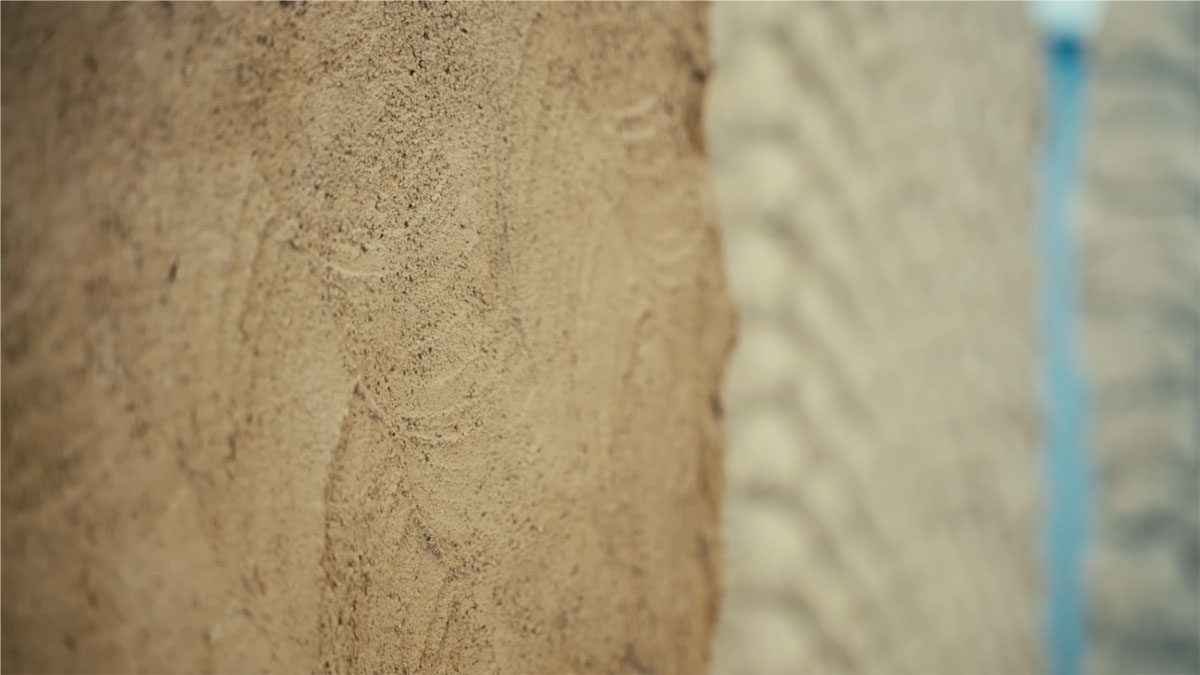
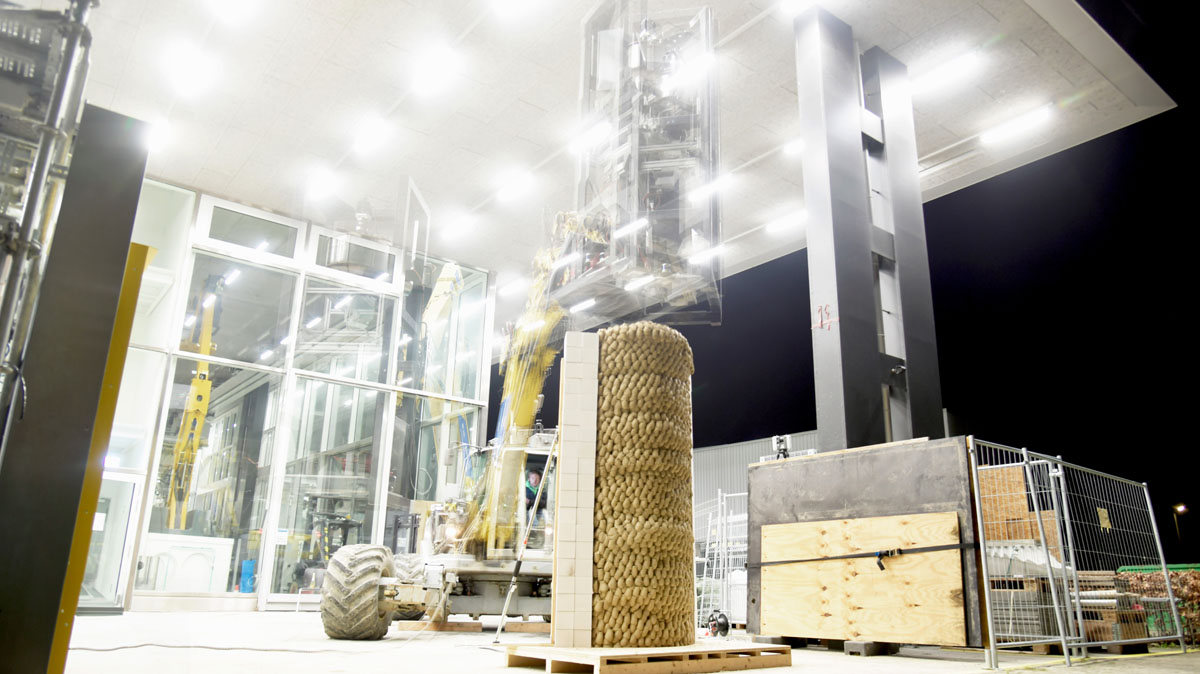
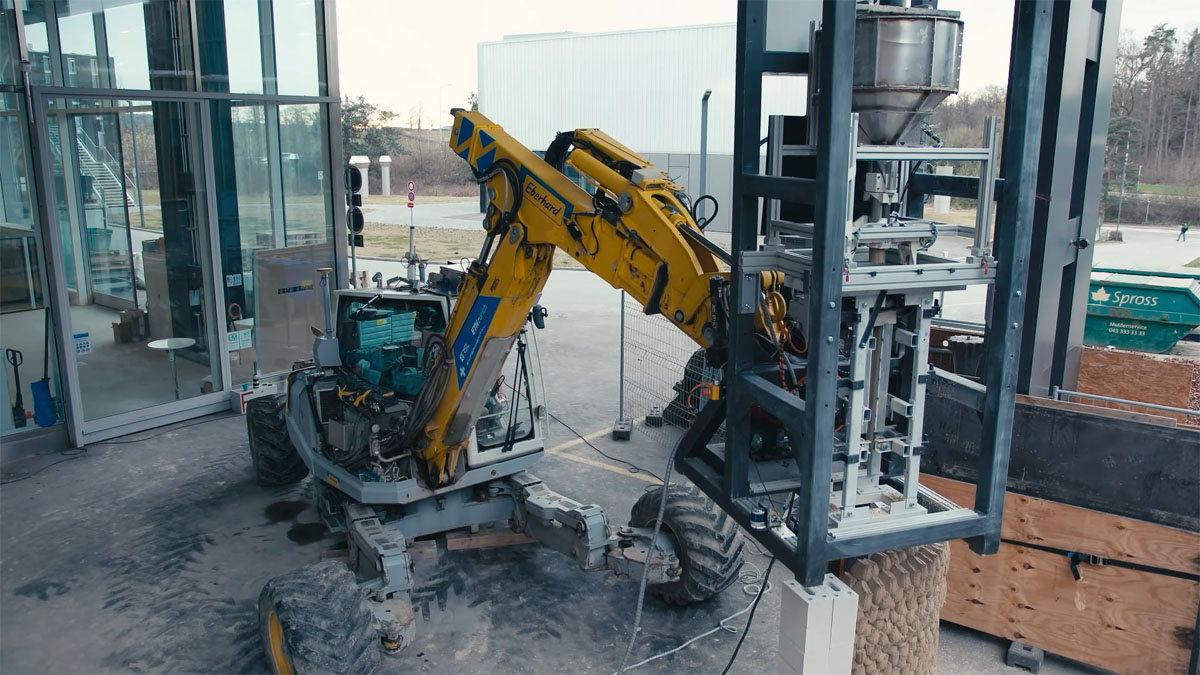
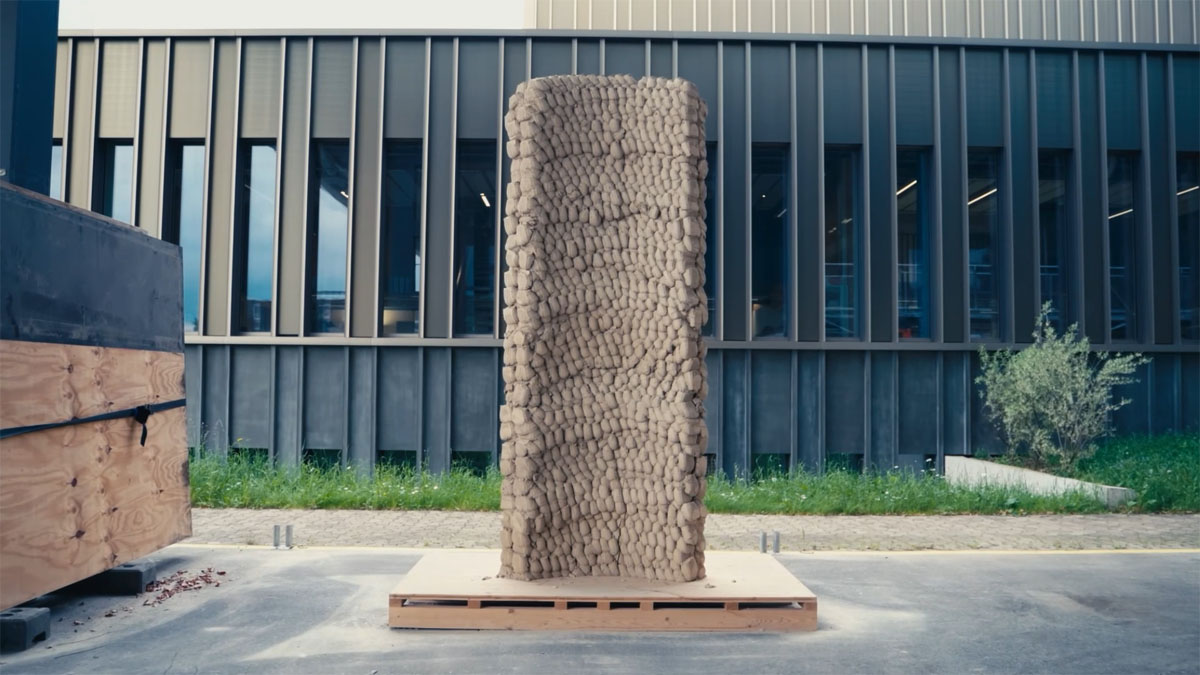
Related Stories
3D Printing | Apr 17, 2017
The Tokyo Pod Vending Machine resembles a giant game of Tetris in the sky
The building is designed to print and dispense its own dwellings in vending machine-obsessed Tokyo.
University Buildings | Oct 19, 2016
UC Merced to nearly double its size by 2020
Its growth strategy includes adding 1.2 million sf of space for teaching, housing, and research.
3D Printing | Jun 14, 2016
By 2021, 3D concrete printing is projected to be a $56.4 million industry
The 3D concrete printing industry is expected to more than double in size within the next five years.
3D Printing | May 26, 2016
Dubai opens world’s first 3D-printed office
The 2,690-sf structure took 17 days to print. City officials say the labor cost was only half as much as similar size conventional buildings.
3D Printing | Mar 29, 2016
Autodesk’s Project Escher prints large objects in fraction of the time
By networking 3D printers and divvying up the work, the project creates big items 80% to 90% more efficiently.
3D Printing | Feb 23, 2016
University of Tokyo students develop 3D-printing pen
The pen, which melts and strings together plastic filaments, can be used to make large-scale temporary structures.
3D Printing | Feb 11, 2016
Microscape mini 3D models give you the whole city in your hands
Starting with Manhattan, the company hopes to expand to other cities, villages, and "suburban cul-de-sacs" with its detailed, 3D models.
3D Printing | Jan 25, 2016
Architecture students create new method for 3D printing concrete
The team's Fossilized project allows for structures that are more varied and volumetric than other forms so far achieved.