Skanska, one of the industry’s leading construction management firms, is finally seeing some easing in inflation and lead times for certain building materials. But pricing and supply remain under increasing demand pressure from sectors like Science + Technology and Mission Critical, that is not likely to abate in 2023.
On November 10, a webinar featuring five of Skanska’s supply-chain, marketing, and account management specialists presented the firm’s latest Construction Market Trend Outlook, which focused on its work in the S+T sector.
In her opening remarks, Director of Strategy Sarah Vakili recounted October’s improvements in the nation’s employment and the Consumer Price Index, which have led Skanska to conclude that any economic recession would likely be relatively mild and short.
The firm expects construction spending in six sectors—manufacturing, highways, transportation, multifamily housing, lodging, and communications—to expand by at least 5 percent next year. Four other sectors—healthcare, public safety, education, and commercial—are expected to grow by 0 to 4 percent. Skanska predicts construction spending will decline for single-family housing, power, improvements, and office buildings.
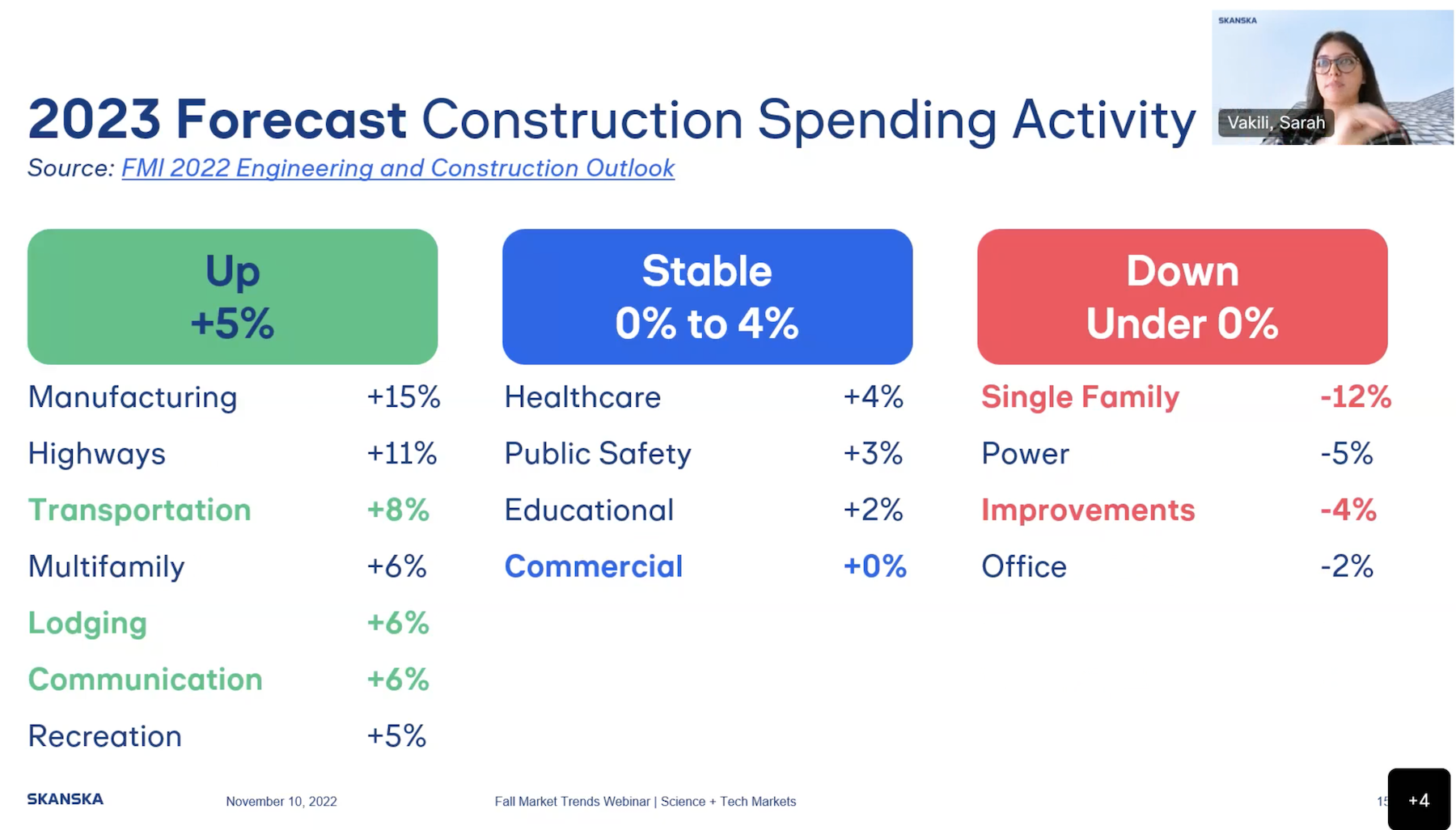
Tom Park, the firm’s Vice President of National Strategic Supply-Chain in Orlando, Fla., noted that a “sharp reduction” in housing starts has eased material demand. He added that lead times have also shortened in some commodities: for example, structural steel, whose lead time peaked at 48 weeks, is now down to 26 weeks, with pricing trending downward, too. Commercial roofing materials, which not too long ago took a year to receive, are now down to between 30 and 36 weeks, with pricing leveling off.
Lead times for other materials—architectural interiors, lumber, and plumbing—also shrank. In the case of plumbing pipe, Park explained that the availability of raw materials has recovered, production has stepped up, and residential construction demand has lessened.
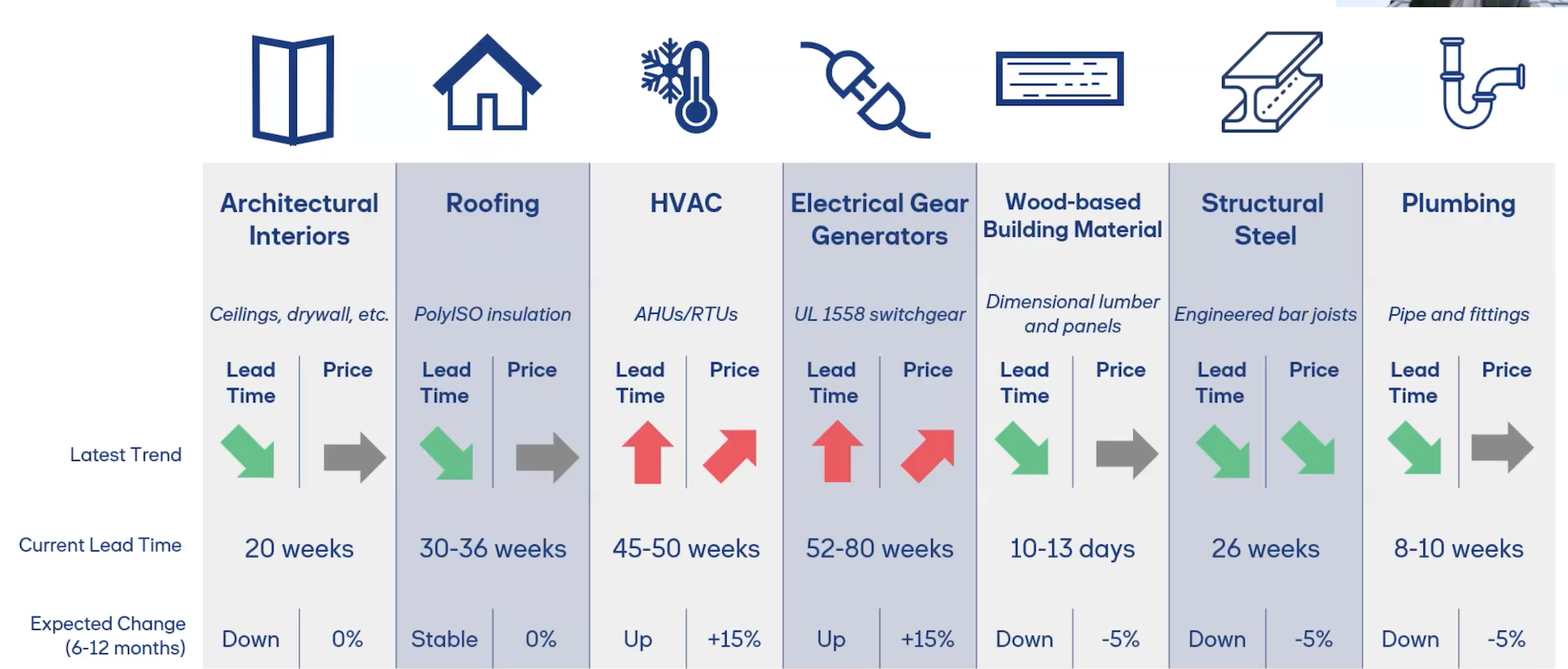
Park pointed out, though, that lead times remain protracted for two commodity categories—HVAC and electrical gear generators. HVAC manufacturers are struggling to fill 12- to 18-month backlogs. And the four gear manufacturers in the U.S. are receiving what Park calls “unprecedented demand” from data center providers that are willing to sign long-term purchase agreements, as well as demand from the S+T and automotive sectors. Skanska expects pricing for HVAC and electrical products to rise by as much as 15 percent next year. And Park doesn’t expect lead times for either to recede for another two to three years, which is why Skanska has been recommending to its clients that equipment be part of early-release packages.
A thriving market for more lab space
Tieg Murray, Skanska’s Pennsylvania-based Director of Market Strategy, used her time in the webinar to provide an overview of the S+T market sector, which she described as “still extremely strong.” (Skanska currently has 19 S+T experts across the country.) Murray saw four factors fueling demand in this sector: the Biden Administration’s $2 billion National Biotechnology and Biomanufacturing Initiative, supply-chain snags that are reopening domestic distribution channels, large-scale pharmaceutical manufacturing, and cell and gene therapy pipelines.
Quoting CBRE, Murray noted that lab space construction in the second quarter of 2022 increased, year-over-year, by 65.6 percent to 31.3 million sf, with the greatest amount of that construction occurring in tech hubs Boston/Cambridge, San Francisco, and San Diego. Over the next 18 months, 26.6 million sf of lab space are expected to be added. Quoting Cushman & Wakefield estimates, Murray stated that 60 percent of the new S+T construction in 2022 was pre-leased.
Murray cited a recent CRB survey of Life Sciences companies about how they planned to expand their lab/cGMP spaces over the next five years. Nearly eight of 10 respondents, 78 percent, will add space through renovation; another 63 percent said preconstructed spec space will fill their needs.
Murray also noted that there are 63,000 active clinical trials in the U.S., 40 percent of which are in Phase III, which is when suppliers typically start investing in manufacturing facilities to convert research into product.
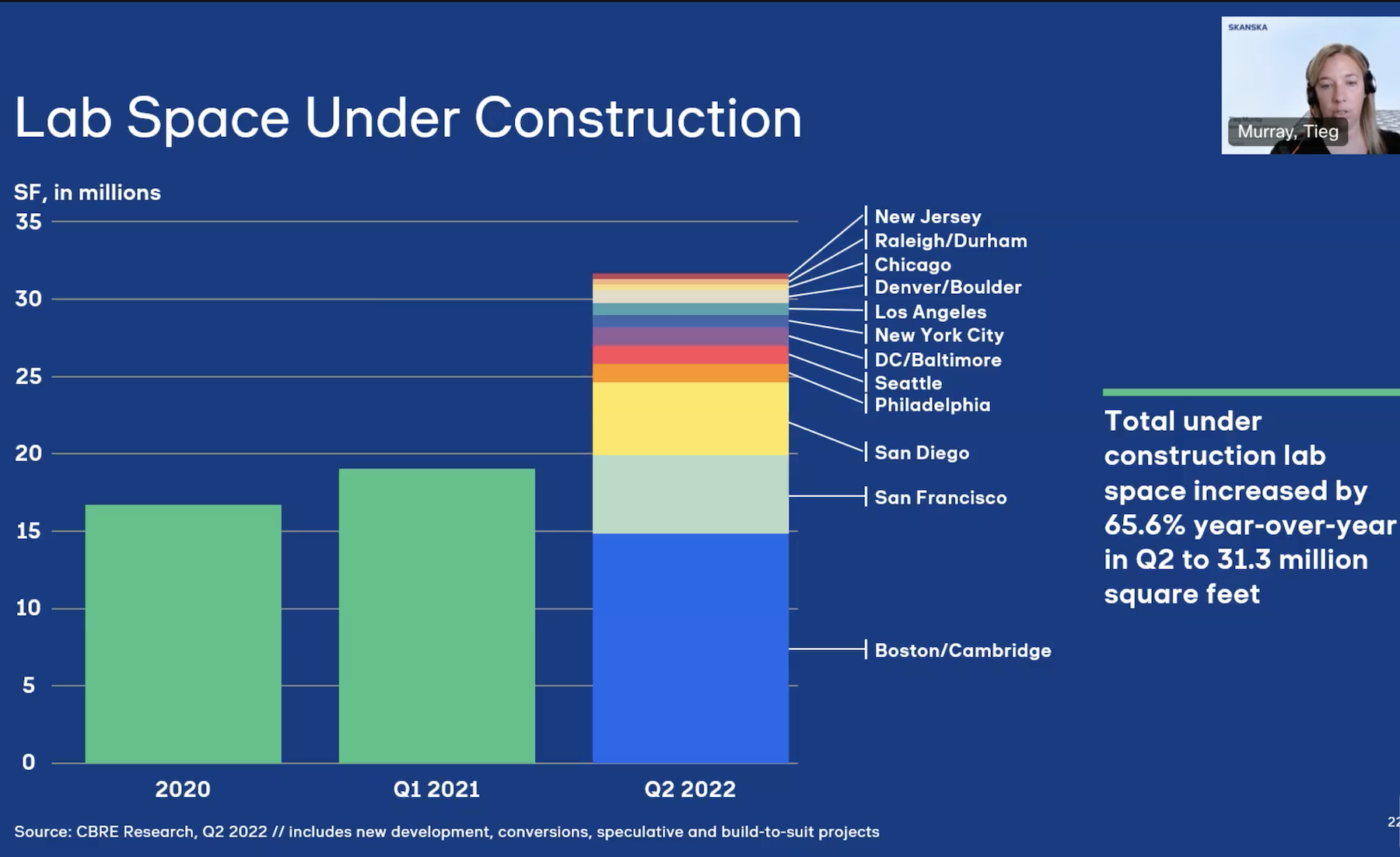
More markets craving data centers
According to the market research firm Arziton Advisory and Intelligence, the data center construction market in the U.S. is projected to grow at a 3.5 percent annual clip, reaching around $25 billion in spending and 20.07 million sf by 2027.
Cloud and colocation providers continue to expand, said Kevin Connor, Skanska’s Vice President and account manager in Phoenix, whose focus is on data center clients. Connor referred to 2022 as “the mega building year” in this sector whose development has been slowed, but not stopped, by supply-chain issues. A bigger problem for providers, said Connor, has been access to labor for construction projects that can require 200-300 electricians over a 12- to 16-month period.
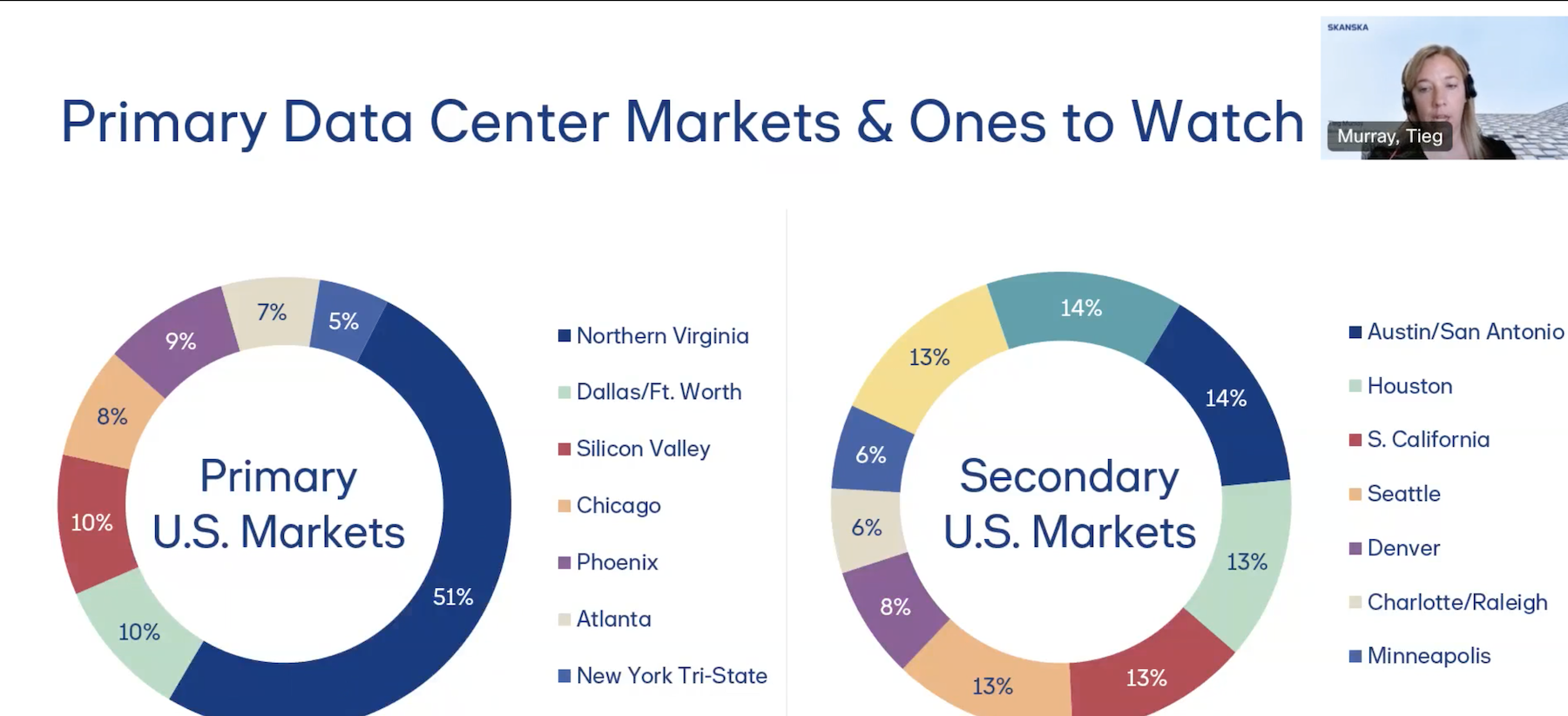
Given the velocity of construction in this sector, Skanska has positioned itself as a “watchdog” over project quality, said Connor. He saw other opportunities for his firm in preconstruction engagement to help clients control their projects’ scheduling and costs.
The same holds true for S+T and Life Sciences, said Theo Diamantis, Skanska’s Vice President and account manager in New York, who discussed how her firm helps clients corral price escalation, especially on large projects. (One of her recent jobs is a $1.4 billion upgrade and expansion of Regeneron Pharmaceutical’s campus in Tarrytown, N.Y.)
Diamantis said that Skanska tries to dissuade clients from coming up with budgets on their own (a not-uncommon occurrence, she implied) without consulting their AEC partners because those estimates usually fall short of the actual costs. To get a handle on prices and lead times, Diamantis said that some clients are buying and storing materials earlier, and are exploring “open shop” (i.e., non-union) labor options. For mega projects, Skanska encourages clients to account for price escalation throughout the procurement periods.
Over the past few years, clients have been repositioning their unused office spaces to labs. Diamantis explained that such conversions need to take into consideration infrastructure requirements for lab spaces, floor-to-ceiling heights, electrical and ventilation redundancies, and the structural capacity of the building.
She pointed to one successful recent conversion that didn’t involve an office at all, but a 125,000-sf book warehouse in Ohio that was adapted for labs.
Related Stories
MFPRO+ Research | Oct 15, 2024
Multifamily rents drop in September 2024
The average multifamily rent fell by $3 in September to $1,750, while year-over-year growth was unchanged at 0.9 percent.
Contractors | Oct 1, 2024
Nonresidential construction spending rises slightly in August 2024
National nonresidential construction spending increased 0.1% in August, according to an Associated Builders and Contractors analysis of data published today by the U.S. Census Bureau. On a seasonally adjusted annualized basis, nonresidential spending totaled $1.22 trillion.
The Changing Built Environment | Sep 23, 2024
Half-century real estate data shows top cities for multifamily housing, self-storage, and more
Research platform StorageCafe has conducted an analysis of U.S. real estate activity from 1980 to 2023, focusing on six major sectors: single-family, multifamily, industrial, office, retail, and self-storage.
Student Housing | Sep 17, 2024
Student housing market stays strong in summer 2024
As the summer season winds down, student housing performance remains strong. Preleasing for Yardi 200 schools rose to 89.2% in July 2024, falling just slightly behind the same period last year.
MFPRO+ Research | Sep 11, 2024
Multifamily rents fall for first time in 6 months
Ending its six-month streak of growth, the average advertised multifamily rent fell by $1 in August 2024 to $1,741.
Contractors | Sep 10, 2024
The average U.S. contractor has 8.2 months worth of construction work in the pipeline, as of August 2024
Associated Builders and Contractors reported today that its Construction Backlog Indicator fell to 8.2 months in August, according to an ABC member survey conducted Aug. 20 to Sept. 5. The reading is down 1.0 months from August 2023.
Construction Costs | Sep 2, 2024
Construction material decreases level out, but some increases are expected to continue for the balance Q3 2024
The Q3 2024 Quarterly Construction Insights Report from Gordian examines the numerous variables that influence material pricing, including geography, global events and commodity volatility. Gordian and subject matter experts examine fluctuations in costs, their likely causes, and offer predictions about where pricing is likely to go from here. Here is a sampling of the report’s contents.
Contractors | Aug 21, 2024
The average U.S. contractor has 8.4 months worth of construction work in the pipeline, as of July 2024
Associated Builders and Contractors reported today that its Construction Backlog Indicator held steady at 8.4 months in July, according to an ABC member survey conducted July 22 to Aug. 6. The reading is down 0.9 months from July 2023.
MFPRO+ Research | Aug 9, 2024
Apartment completions to surpass 500,000 for first time ever
While the U.S. continues to maintain a steady pace of delivering new apartments, this year will be one for the record books.
Contractors | Aug 1, 2024
Nonresidential construction spending decreased 0.2% in June
National nonresidential construction spending declined 0.2% in June, according to an Associated Builders and Contractors analysis of data published today by the U.S. Census Bureau. On a seasonally adjusted annualized basis, nonresidential spending totaled $1.21 trillion. Nonresidential construction has expanded 5.3% from a year ago.