The Situation:
The City of Tampa is known as a major business hub and tourist attraction that boasts many well-known amusement parks and museums, as well as having the largest bay port in the state. However, this wasn’t always what Tampa was known for. Dating back to the late 1800s, Tampa was nicknamed the “Cigar City” as Cuban and Spanish immigrants moved in and began a prosperous cigar manufacturing community known as the iconic Ybor City.
Over the years, Tampa has gained a spot among the top largest cities in Florida as visitors turn into residents and companies relocate to the burgeoning town. As Tampa began to flourish, the demand for more housing, entertainment, restaurants and shopping (to name a few) began to arise. In 2016, plans for a new 56-acre mixed-use development, Water Street Tampa came underway. The community would sit east of downtown and be one of the largest urban real estate developments currently in the nation. The goal was to develop a brand new, high-profile neighborhood that would unite Tampa’s central business district with the waterfront and neighboring communities.
In an effort to transform the city in a thoughtful and sustainable way, Water Street Tampa unveiled plans to build an innovative district cooling facility amidst the new mixed-use development. The centralized building would reduce redundant mechanical systems and energy consumption. It also would free up the rooftop space often occupied by individual cooling towers to make available space for more amenities or businesses.
Creative Contractors’ Jason Woods, Baker Barrios Architects’ David Del Tosto and Trane air-conditioning company hit the ground running as they worked together to create an intelligently-designed cooling plant that would significantly improve the neighborhood’s infrastructure and promote sustainability. The team went through more than six design iterations before landing on the idea to pay homage to Tampa’s history of cigar factories by bringing the ‘old’ into a brand new modern development. The new building’s brick veneer and historical context would emulate and reflect the heritage of the cigar factory and the immigrants who have shaped Tampa into what it is today.
Since the chiller building is entirely composed of concrete and framing, an industry leading team was needed to provide unique, reliable and competitive thin brick options. The general contractor tapped Bob DiPietro with FSS Company to present a variety of options to the team.
“Once the general contractor told me about the project, they mentioned that they also needed a system in place to help keep brick from falling off a massive screen wall since it was located in a high pedestrian traffic area. I immediately called our LATICRETE Sales Representative, Joe Still. We knew that with a project of this size, only LATICRETE® products could guarantee that the brick would stay in place and not fail to adhere to the wall,” said DiPietro.
The Challenges:
- High Visibility: Since the Chiller Plant would be the first project built in the Water Street Channelside district and it sits in prime view of the Lee Roy Selmon Expressway, thousands of eyes would be on the Chiller Plant building daily. The most important element of the project was designing a structure that captured the historic look of the cigar factory and heritage of the area while bringing the old world into the modern day.
- Architecturally Difficult: Since the building had no roof, there was a tremendous amount of screening that went into the building. The teams underwent special design work so that the walls and corners would be secure, which resulted in the creation of a 33-foot [10 m] tall screen wall, a concrete frame that sits below the cooling tower and a 10-inch [250 mm] steel structure that kicks back through the walls to support the building. The screen wall was seamlessly integrated into the design with relief and arches that resembled a cigar factory. In addition, the building was located in a high velocity wind zone, so the building would need to sustain a minimum of 150 mph (241 kmh) winds.
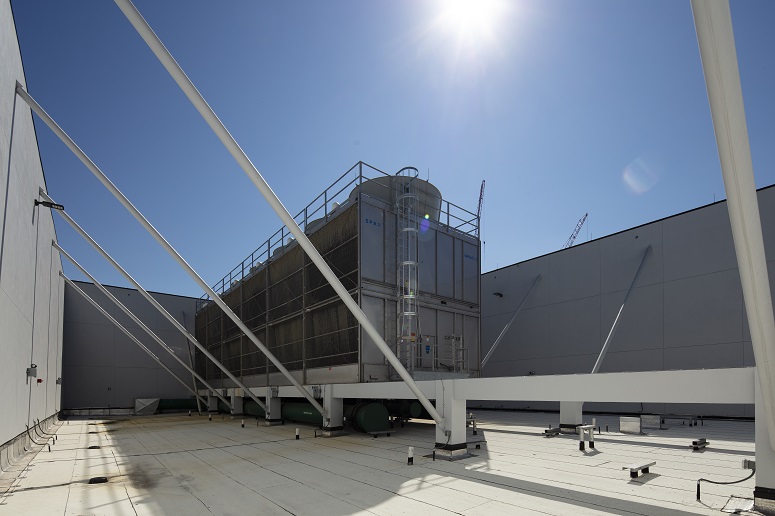
A LATICRETE Solution:
“None of my colleagues in the industry have seen a 33-foot [10 m] tall screen wall before, so it was crucial to have a reliable installation method to apply thin brick veneer, which is only half the thickness of normal brick, on this unique building. My main focus was to create a seamless look between substrates, which required an almost perfect execution in installing a completely flat wall,” said Still.
All of these factors made the decision to have contractor Masonry Builders install the LATICRETE Masonry Veneer Installation System (MVIS™) simple. The MVIS products are designed to deliver superior, long-term performance on thin-brick, manufactured stone and natural stone veneers for interior and exterior applications. The complete system includes air and water barrier products, reinforcing fabrics, various polymer fortified adhesive mortars that provide non-sag performance, as well as a pointing mortar and LATASIL™ sealant.
Due to the thin brick’s vast area of exposure, air and water barriers were vital to prevent weather related damage. Unlike traditional on-site mortar mixes that are subject to large variations in standards, MVIS is engineered to provide a permanent, high-strength solution that is high velocity wind zone tested and protects structures against water intrusion. This made the MVIS Air & Water Barrier a perfect match as it bonds directly to the substrate with ease, thanks to its excellent bond strength. It contains a low VOC, self-curing formula with antimicrobial technology and is ideal for construction projects where air and water barriers are required to improve building efficiency and durability.
When the suitable masonry substrate was in place and leveled to the specified plane to receive the adhered veneer, the installer applied the MVIS air and water barrier. Then, a thin brick adhesive mortar was used to install the custom-made thin brick.
Once the thin brick set firm, the Masonry Builders team finished up by applying the MVIS Premium Pointing Mortar, a high-performance pointing mortar, was used to point the joints. Lastly, LATASIL sealant, a high-performance, neutral cure, 100% silicone sealant designed for ceramic tile and stone applications, was used for all of the control joints.

“I was called into this project because there was a need to have an installation method to install veneer on a rather unique building. With our MVIS products and proper design and consideration, we were able to get the system delivered for this project with a fair degree of certainty that all of the installed material would stay there,” added Still.
Outcome:
Completed in January 2020, the 12,500-square-foot [1161 square meters] Chiller Plant, which hosts an excess of 30,000-square feet [2787 square meters] of thin brick and an entire field of ice makers, has proven to be 30 to 40 percent more environmentally sustainable compared to having traditional individual chiller systems on each building throughout the new Water Street Tampa development. The completed plant contains 11 pumps, six cooling towers and three chillers, with additional space for more to be added in the future.
In addition, thanks to the LATICRETE MVIS products, the building more than met the high velocity wind zone requirement of sustaining a minimum of 150 mph (241 kmh) after having passed the Miami-Dade hurricane test at 205 mph (330 kmh). The new district cooling plant also contributes to the WELL Community Standard requirements.
“As our city continues to grow, we have to make sure we’re doing so in a thoughtful way. This district cooling facility will play a big role in reducing our energy consumption while we work to create a more sustainable and resilient city,” said Mayor Jane Castor. “This is a big step forward in the right direction as we continue transforming Tampa together.”
GC/Builder
Creative Contractors
Clearwater, Florida
Architect
Baker Barrios Architects
Orlando, Florida
Contractor
Masonry Builders, Inc.
Tampa, Florida
Distributor
FSS Company
Plant City, Florida
Thin Brick Manufacturer
Marion Ceramics, Inc.
Marion, South Carolina
LATICRETE International Inc.
https://laticrete.com/
Bob Duke
Regional Sales Manager, SPD
(203) 231-8380
rwduke@laticrete.com
Related Stories
| Feb 22, 2011
New EcoSpec Tile company offers recycled tiles
EcoSpec Tile LLC, established February 1, 2011, is a new tile manufacturing company started by a group consisting of experienced/time-tested tile professionals who collectively feel a strong responsibility to their industry and to their planet. The initial product offering includes sustainable tile material composed of 50% pre-consumer waste, 20% post-consumer waste and 30% new material recycled contents.
| Jan 21, 2011
Sustainable history center exhibits Fort Ticonderoga’s storied past
Fort Ticonderoga, in Ticonderoga, N.Y., along Lake Champlain, dates to 1755 and was the site of battles in the French and Indian War and the American Revolution. The new $20.8 million, 15,000-sf Deborah Clarke Mars Education Center pays homage to the French magasin du Roi (the King’s warehouse) at the fort.
| Jan 21, 2011
Library planned for modern media enthusiasts
The England Run Library, a new 30,000-sf glass, brick, and stone building, will soon house more than 100,000 books and DVDs. The Lukmire Partnership, Arlington, Va., designed the Stafford County, Va., library, the firm’s fourth for the Central Rappahannock Library System, to combine modern library-browsing trends with traditional library services.
| Dec 17, 2010
Subway entrance designed to exude Hollywood charm
The Hollywood/Vine Metro portal and public plaza in Los Angeles provides an entrance to the Red Line subway and the W Hollywood Hotel. Local architect Rios Clementi Hale Studio designed the portal and plaza to flow with the landmark theaters and plazas that surround it.
| Dec 17, 2010
Cladding Do’s and Don’ts
A veteran structural engineer offers expert advice on how to avoid problems with stone cladding and glass/aluminum cladding systems.
| Oct 13, 2010
Hospital tower gets modern makeover
The Wellmont Holston Valley Medical Center in Kingsport, Tenn., expanded its D unit, a project that includes a 243,443-sf addition with a 12-room operating suite, a 36-bed intensive care unit, and an enlarged emergency department.
| Oct 12, 2010
Holton Career and Resource Center, Durham, N.C.
27th Annual Reconstruction Awards—Special Recognition. Early in the current decade, violence within the community of Northeast Central Durham, N.C., escalated to the point where school safety officers at Holton Junior High School feared for their own safety. The school eventually closed and the property sat vacant for five years.
| Oct 12, 2010
Richmond CenterStage, Richmond, Va.
27th Annual Reconstruction Awards—Bronze Award. The Richmond CenterStage opened in 1928 in the Virginia capital as a grand movie palace named Loew’s Theatre. It was reinvented in 1983 as a performing arts center known as Carpenter Theatre and hobbled along until 2004, when the crumbling venue was mercifully shuttered.
| Oct 12, 2010
The Watch Factory, Waltham, Mass.
27th Annual Reconstruction Awards — Gold Award. When the Boston Watch Company opened its factory in 1854 on the banks of the Charles River in Waltham, Mass., the area was far enough away from the dust, dirt, and grime of Boston to safely assemble delicate watch parts.
| Oct 12, 2010
Cuyahoga County Soldiers’ and Sailors’ Monument, Cleveland, Ohio
27th Annual Reconstruction Awards—Gold Award. The Cuyahoga County Soldiers’ and Sailors’ Monument was dedicated on the Fourth of July, 1894, to honor the memory of the more than 9,000 Cuyahoga County veterans of the Civil War.