APA’s Compelling Conversations features building professionals discussing important issues with APA experts and what they mean for the building industry. In this edition, APA Engineered Wood Specialist Ron Nuttall interviews Ross Cohen, the president of Littleton, Colorado-based DL Cohen Construction Co. LLC. DL Cohen is a commercial wood framing contractor that specializes in large, multifamily projects. DL Cohen says it offers a level of service and quality unavailable in traditional framing. Ross Cohen explains why the company prefers panelized walls to other framing methods.
Ron Nuttall: What led your company to adopt panelized walls?
Ross Cohen: The first reason for moving away from traditional site-built/stick framing to off-site-built components was to ensure complete and correct construction to create “trade-ready” floors as multifamily buildings are constructed.
We believe that product compliance and build schedules have all become increasingly demanding. Relative to historically built 1- and 2-story single-family homes, the multifamily projects — some even 5-stories — feature dramatically more complex requirements like fire separations, 5-story stacked framing and demanding shear detailing. At the same time, qualified trade workers have been exiting the market. We decided to use comprehensive modeling and associated manufacturing processes to fabricate framing elements off-site — moving away from a craftsman-based industry to one that is controllable and scalable.
Ron: What are the advantages of using panelized walls with continuous wood structural panel sheathing?
Ross: Site-built or factory-built, the sheathing specification is typically unchanged. At the factory, sheathing is applied to wall panels. It offers a chance to optimize the sheathing specification with holistic shear design analysis. At the factory, nailing patterns are executed with far greater control which enables efficient specification by EOR. Most importantly, however, oriented strand board (OSB) stores and ships well in a bundle of panelized exterior walls.
Ron: What other engineered wood products besides wood structural panels do you use?
Ross: We recently changed our headers to a solid LVL (laminated veneer lumber), away from multiple plies of dimensional lumber. We switched from two 2x10 headers to a single 3 ½-inch LVL header because it streamlines production. The 2x10s need a filler piece to make the header thickness match the wall framing. They have to be gang-nailed together. We also can use a 7 ¼-inch deep LVL versus the 2-by-10s, which are 9 ¼ inches — meaning less wood mass in the wall component.
Ron: Let’s compare panelization to traditional in-field installation. How does it differ in terms of time?
Ross: With approximately half as many field wall assemblers, schedules are dramatically reduced by assembling off-site-built walls compared with site building/stick framing walls. Interestingly, one of the larger schedule improvements is eliminating traditional detail snapping of walls on a subfloor.
Ron: What about quality?
Ross: The quality of an off-site-built product is incomparably better than a traditional site-built product, because:
- All structural members are cut on automated saws that inkjet mark and cut to a 64th of an inch.
- All project sub-elements are built identically, i.e., doors or windows, shear elements, etc.
- Structural coordination at a level of minutia in vetting the architectural plan occurs in a model as opposed to in the field or on the fly.
- With comprehensive modeling, a singular model for an entire structure, buildings can be constructed in such a fashion as to stack perfectly, i.e., all walls and trusses on top of one another.
Ron: And what about cost?
Ross: Few would suggest that a framer is paid even a nickel more than they were 30 or even 40 years ago for a square foot of framing while the evolutions of code and engineered design of 5-story products has become substantially more complex over the same period. Simultaneously, the cost of lumber materials and framing labor, plus the cost of detailing, structural hardware, safe work expenses, etc., have all increased. Ultimately, we seek to sell a better-constructed product that is built faster without compromising quality or adherence to modern code and engineering standards, with a less embodied carbon model while considering the downstream needs of other trades for the same price, all while meeting or even exceeding deadline expectations for the builder. Additionally, our process enables us to reduce aggregate material usage by approximately 20%, as well as divert over half of our factory-generated waste from landfills.
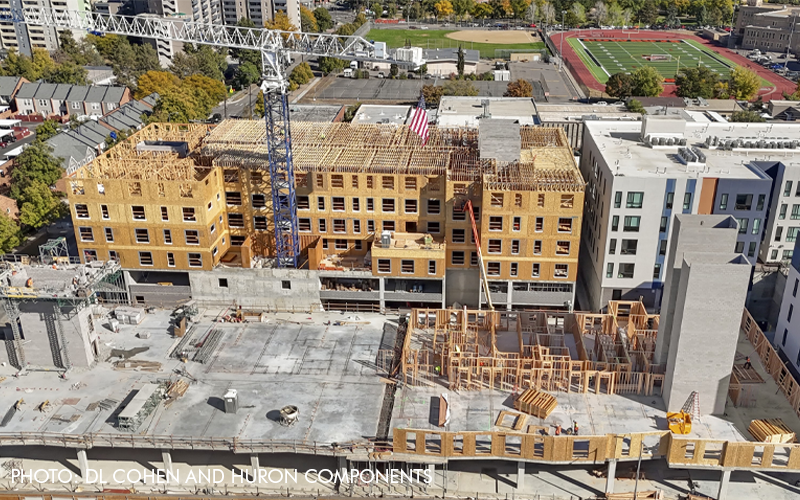
Ron: What challenges or limitations have you encountered with panelization, and how do you mitigate these issues?
Ross: One challenge is a long stretch of wall panels through a corridor or at party walls tend to grow slightly when installed in the field. To fix it, we hold the end studs one-eighth inch from the edge of the panel in our shop. The framer can cut up to an eighth off the top and bottom plate on each side of any wall for minor adjustments without having to adjust any studs. Island heights also tend to grow slightly. We design them a quarter-inch short so that they will be finished at the correct height after nailing everything together. We also sheet one side of the islands with OSB to keep them square throughout construction. We have not met any limitations on the type of wood-framed construction or product presented to us. Panelization really shines with repeatable product types because every unit will be built the same way every time — unlike conventional stick framing.
Ron: How does panelization accommodate changes or modifications that arise during construction?
Ross: We build all wall panels by the bundle, so if a late change occurs, we will make design adjustments and resend the bundles to the shop. The key to success is to have the plans complete and issues worked out in the design phase before going to production. We can also easily change wall panels if a minor field adjustment is needed.
Ron: As a panelizer, can you explain your involvement in the design process?
Ross: The sooner we engage in plan development with our customers, the better. We can always suggest details that result in large value engineering savings for Type III and Type V construction. Our designers also incorporate all architectural, structural, mechanical, electrical and plumbing details. This gives us the ability to catch many architectural and structural problems, such as tubs and showers that don’t fit, loading issues, and much more. The most successful building design will have wall panels, floor trusses, and roof trusses designed in a singular, comprehensive model. When contractors award these phases to different subs, they lose the value of clash detection, stud vs. truss placement, finding plan conflicts, etc.
Ron: What logistics and coordination efforts are required for panelization? How do they compare to in-field installation?
Ross: Panelizing takes more preconstruction efforts to get final rough opening sizes, plumbing submittals, and information from other trades beforehand to ensure everything is incorporated correctly in the design. Another important coordination effort is to match the construction phase for wall production and site delivery as much as possible. Wall panels are all built and shipped per bundle, so it’s easy to match which areas a framer needs to receive on-site and the timing of our deliveries. Panel framing schedules are also very fast-paced compared with stick framing. We build panels up to a month ahead to avoid any unforeseen site conditions or weather delays.
In today's construction, the dialogue between innovation and tradition helps advance the industry. DL Cohen Construction Co. LLC's decision to adopt engineered wood products and modern techniques highlights a shift in the industry towards prioritizing improved efficiency, quality and sustainability.
Interested in incorporating panelized wall systems into your next construction project? Contact your local APA Engineered Wood Specialist today for a complimentary consultation.