Get ready for a surge in prefabrication activity by contractors.
FMI, the consulting and investment banking firm, recently polled contractors about how much time they were spending, in craft labor hours, on prefabrication for construction projects. More than 250 contractors participated in the survey, and the average response to that question was 18%. More revealing, however, was the participants’ anticipation that craft hours dedicated to prefab would essentially double, to 34%, within the next five years.
The study—a sequel to FMI’s 2023 Labor Productivity Study—reiterates how the industry’s receptivity to prefab solutions corresponds with its ongoing labor shortages and compressed project schedules. (Contractors experienced approximately $30 billion to $40 billion in lost profits due to labor inefficiencies in 2022.) In its latest study, contractors told FMI that “improved quality” was prefab’s greatest perceived benefit. “Reducing the risk and variability” is how one contractor put it. Other benefits cited include reductions in construction schedules and improved worker safety.
(Nearly three fifths of the respondents to FMI’s study are MEP contractors, with another 15% being framing and drywall contractors.)
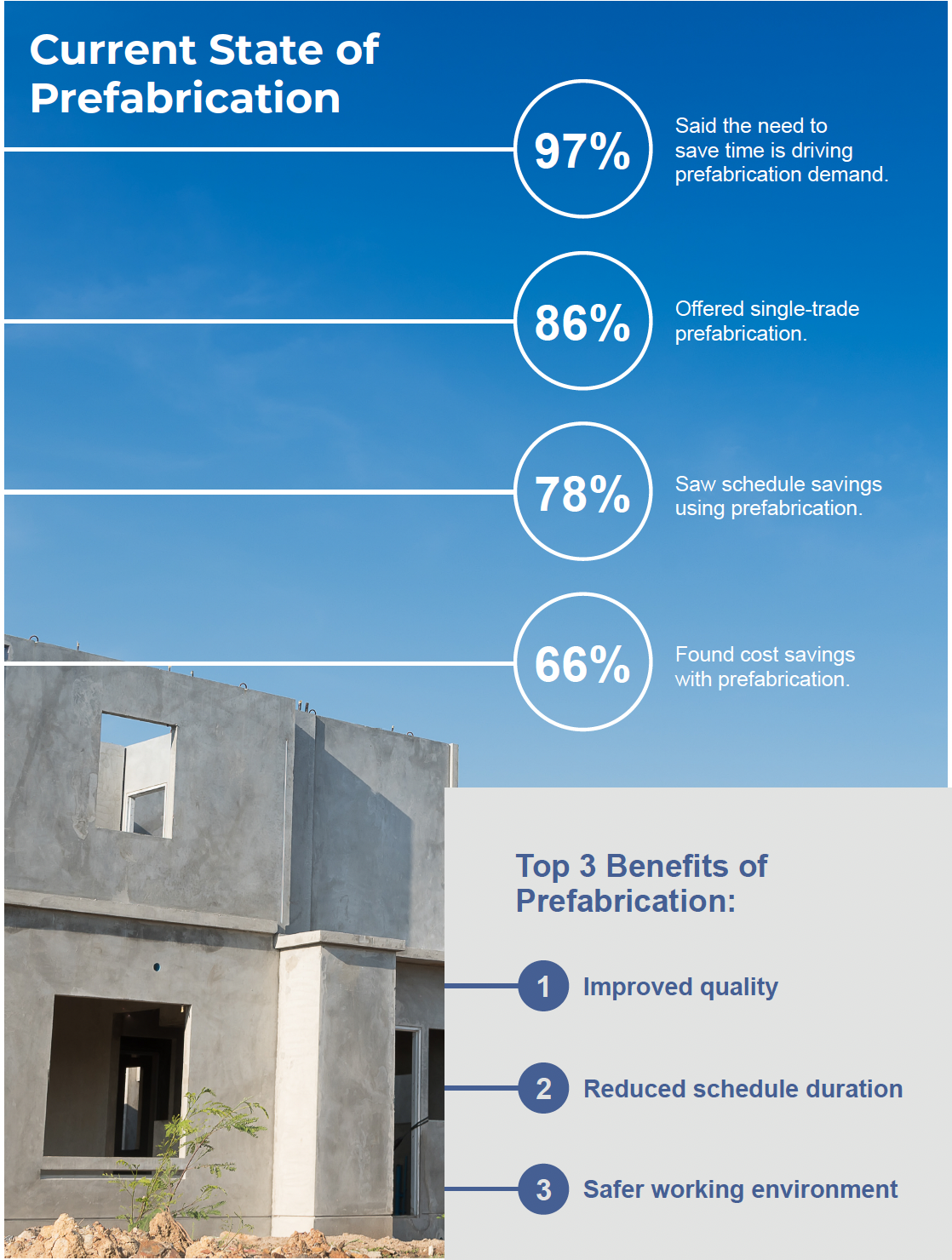
Contractors that consider prefabrication must determine how to do it at scale, profitably, and in a way that increases company earnings. Successful prefab practices, says FMI, require long-term strategic thinking and planning across an organization, along with the development of a comprehensive operational blueprint.
Which prefab model is right for pros?
It’s not like prefabrication is an alien concept for contractors. FMI’s study found that 86% of respondents currently offer single-trade prefab services. Three quarters of the concrete contractors surveyed said they are prefabricating on their jobsites; 57% of self-performing general contractors polled are prefabbing on-site, too.
What’s often lacking, however, is a clear vision of what they want their prefab capabilities to become. To make prefab work, says FMI, contractors need to shift their operating models, processes and systems. Contractors also need to decide which prefab models and combinations would work best for their companies; these include kitting services, multi-trade services, procurement, and modular services.
In making these determinations, contractors should be asking themselves:
•Why do we want to do more prefabrication?
•What is the total addressable portion of our work mix (today) that could be prefabricated?
•What investments would need to be made to scale our prefabrication capabilities to capture that opportunity?
•When fully optimized, what does the earnings stream from prefabrication look like?
•What does the return on investment look like for the enterprise?
•Do we have alternative investment options for other initiatives in the business? How do those options stack up against our prefabrication ambitions?
•Will prefab make the company better, more profitable, and resilient?
Prefabrication a different kind of business
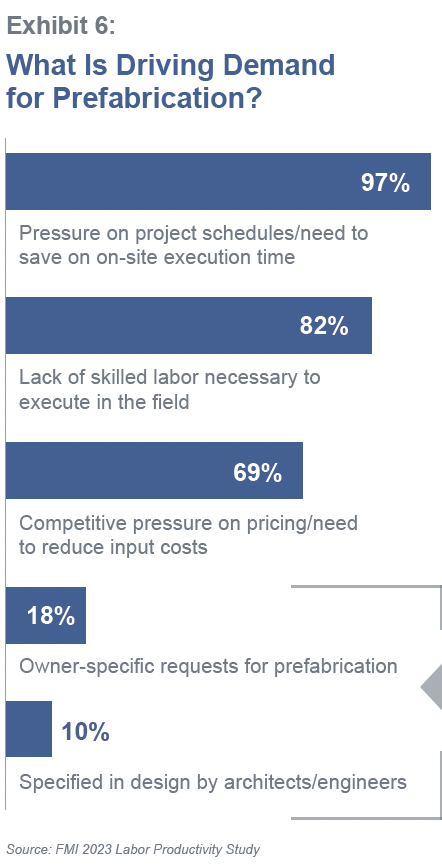
Prefabrication is a manufacturing endeavor that’s different from building construction. Contractors diving into prefab in a bigger way need to think about whether prefab will be a unique business or separate entity, and how autonomously construction and prefabrication operate? Will prefab services be proprietary or available to other contractors? Will prefab be a profit or cost center? How will manufacturing cost overruns, if there are any, be accounted for?
FMI says that contractors need to establish clear project management lines that encompass how prefabricated products are tracked, stored, and billed for. Tracking labor productivity across prefabrication and field installation is key.
Owners and designers need to buy in more
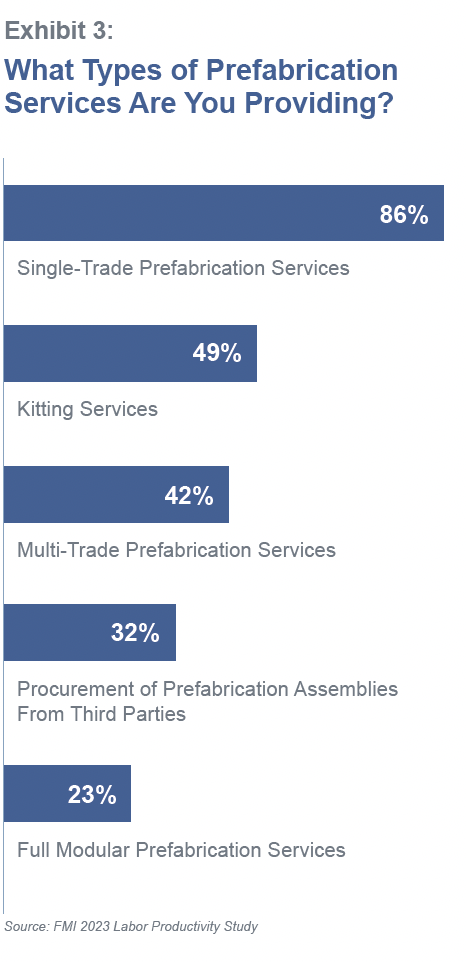
One of the contractors whom FMI polled mentioned a recent casino and hotel project that required 25% less labor in the field, and cut nearly two months off of its installation time, by using prefabrication methods.
Scheduling is driving prefab demand, says FMI. But expanding that demand depends on acceptance by owners and AEC firms, and right now, that acceptance is middling: only 18% of the contractors polled by FMI said that owner-specific requests drove prefab, and only 10% said that prefab was specified by architects or engineers.
“For the industry to realize substantial gains in prefabrication and productivity, owners and designers need to be a bigger part of the demand equation,” says FMI.
FMI’s study found that the industry still struggles with broad adoption. The biggest challenges to adopting prefab are a project’s design and coordination, stakeholder awareness and education, the mindset and culture of a project’s active players, and the investment in facilities and equipment.
But given current and projected labor force limitations, “it’s clear that prefabrication will need to become part of the solution.” For that to happen, building teams need to demonstrate a bolder vision, strategic planning, commitment to investing, consistent communication, and a proactive engagement by external stakeholders.
Related Stories
| Apr 2, 2014
8 tips for avoiding thermal bridges in window applications
Aligning thermal breaks and applying air barriers are among the top design and installation tricks recommended by building enclosure experts.
| Mar 31, 2014
Tips for creating a competitive bid using codes and loads
Landing a project feels like winning a prize, sort of like finding that forgotten $20 bill in the pocket of a pair of jeans you haven’t worn in a while. But living on the “chance” of winning a job isn’t a great way to pay your electric bill. So, how do you swing the chances in your favor?
| Mar 26, 2014
A sales and service showcase
High Plains Equipment, a Case IH dealership in Devils Lake, N.D., constructs a larger facility to better serve its customers.
| Mar 26, 2014
Callison launches sustainable design tool with 84 proven strategies
Hybrid ventilation, nighttime cooling, and fuel cell technology are among the dozens of sustainable design techniques profiled by Callison on its new website, Matrix.Callison.com.
| Mar 20, 2014
Common EIFS failures, and how to prevent them
Poor workmanship, impact damage, building movement, and incompatible or unsound substrate are among the major culprits of EIFS problems.
| Mar 19, 2014
Frames: the biggest value engineering tip
In every aspect of a metal building, you can tweak the cost by adjusting the finish, panel thickness, and panel profile. These changes might make a few percentage points difference in the cost. Change the framing and you have the opportunity to affect 10-20 percent savings to the metal building portion of the project.
| Mar 17, 2014
Rem Koolhaas explains China's plans for its 'ghost cities'
China's goal, according to Koolhaas, is to de-incentivize migration into already overcrowded cities.
| Mar 12, 2014
14 new ideas for doors and door hardware
From a high-tech classroom lockdown system to an impact-resistant wide-stile door line, BD+C editors present a collection of door and door hardware innovations.
Sponsored | | Mar 10, 2014
A high-performance barn
Bastoni Vineyards replaces a wooden barn with an efficient metal building used for maintenance, storage, and hosting events.
| Feb 14, 2014
Must see: Developer stacks shipping containers atop grain silos to create student housing tower
Mill Junction will house up to 370 students and is supported by 50-year-old grain silos.