The phoenix: a mythological bird that symbolizes resurrection, rebirth, and life after death. Demolished in 1989, The Phoenix Ironworks Steel Factory left a five-acre hole in West Oakland, Calif. After sitting vacant for nearly three decades, the site will soon become utilized again as The Phoenix rises from the ashes—this time in the form of 316 affordable housing units.
In a collaboration between MBH Architects, modular construction company Factory_OS, technology provider Autodesk, bio-materials company Ecovative, building envelope consultant Heintges, and fabricator Kreysler & Associates, The Phoenix aims to be a revolutionary development made possible through groundbreaking biomaterials, innovative building methods, and Autodesk’s Design and Make Platform, which connected these teams and their data through cloud-based workflows and provided AI-powered insights.
AI Brings Affordable Housing Project to Life
In the case of The Phoenix, AI played a heavy role in optimizing the design of the affordable housing development.
The team used Autodesk Forma in early-stage design to “rapidly explore a wide range of design options that would simultaneously meet the project’s goals for cost, carbon, and livability,” according to David Benjamin, Director, AEC Industry Futures at Autodesk.
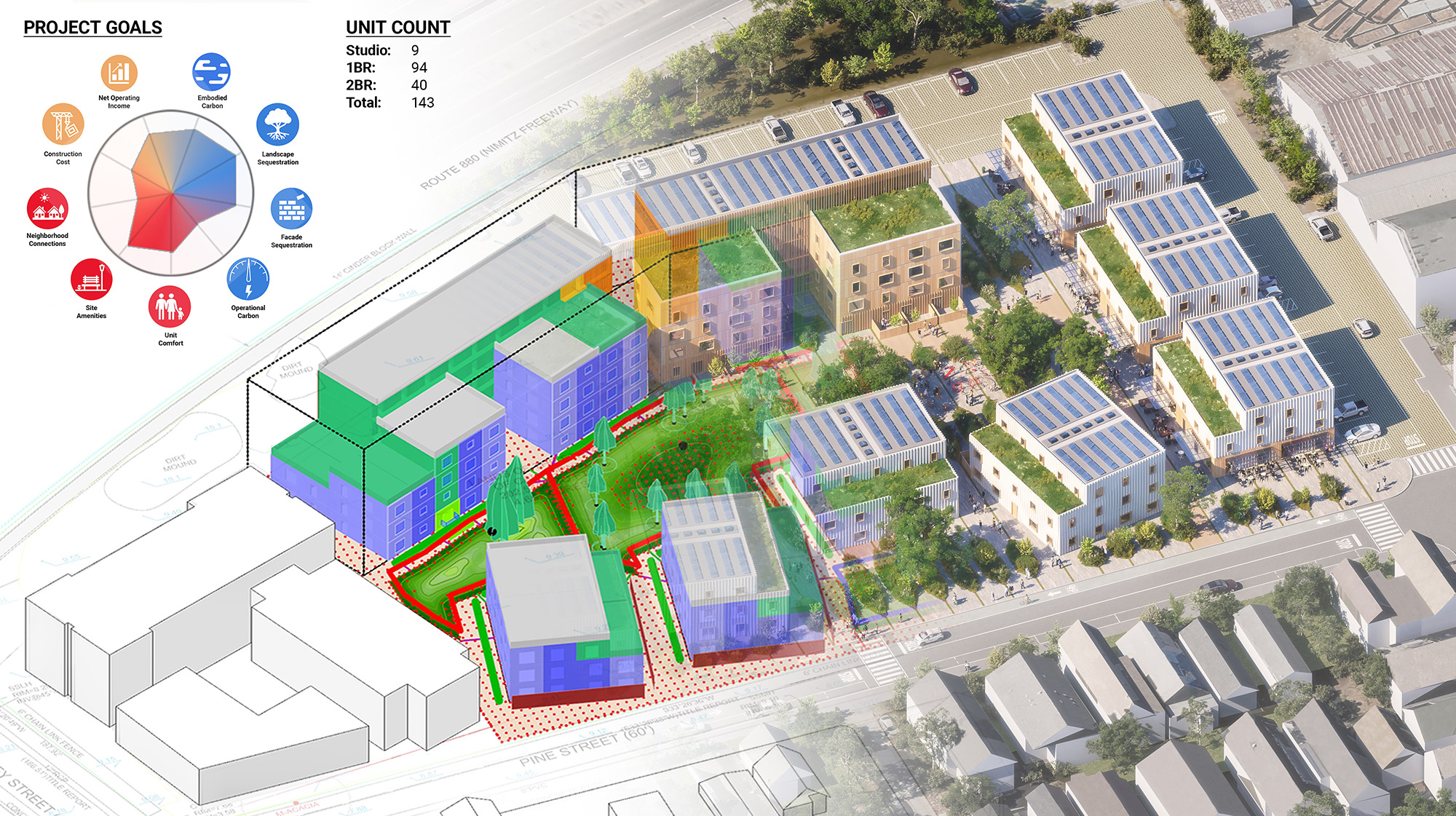
These capabilities allowed MBH to adjust and analyze different multifamily designs—such as adding buildings, or moving around structures and greenspaces—to find the most optimal layout.
One analysis the project team did was to test how different building configurations were affected by noise from nearby highway traffic. With Autodesk Forma’s AI-powered tool, Rapid Noise Analysis, MBH Architects could optimize the final placement of structures on the building site to minimize noise. By using this technology MBH could explore the range of options and was able to complete an initial design package in just six hours—compared to the typical timeframe of two weeks.
“Time saving is probably the biggest benefit of [AI] tools, which enable us to ensure faster delivery of much-needed housing solutions,” says Ryan McNulty, Principal, Architect, MBH Architects.
Autodesk Forma was also used to measure goals for operational and embodied carbon, cost, and livability. The tool helped the team iterate on various designs like relocating playgrounds or shifting buildings to land on a final design that met the needs of the developer, the community, and stakeholders.
![]() | ![]() |
Through this process, The Phoenix is projected to be completed in half the time, cost, and carbon footprint of a typical multifamily housing project in the Bay Area, which made the project eligible for state incentives, according to McNulty. While AI and cloud-based workflows supplied ample time-saving benefits on the front end, volumetric modular construction will present additional cost-effective opportunities once on-site construction begins.
Modular Construction with Innovative Biomaterials
Manufactured by Factory_OS, the modular units of The Phoenix can be assembled in just 10 days, according to MBH. Though this modular construction method speeds up project delivery, reduces waste, and removes the unpredictability of a traditional construction, it’s not without risk. Efficiently wrapping the modular units to ensure the building becomes weather-tight is “an ongoing design challenge,” says McNulty.
While standardizing window sizes has improved efficiency in building unit fabrication, incorporating prefabricated exterior panels introduces a new layer of complexity. The team is focused on systematizing various elements like windows and FRP panels to enable façade prefabrication.
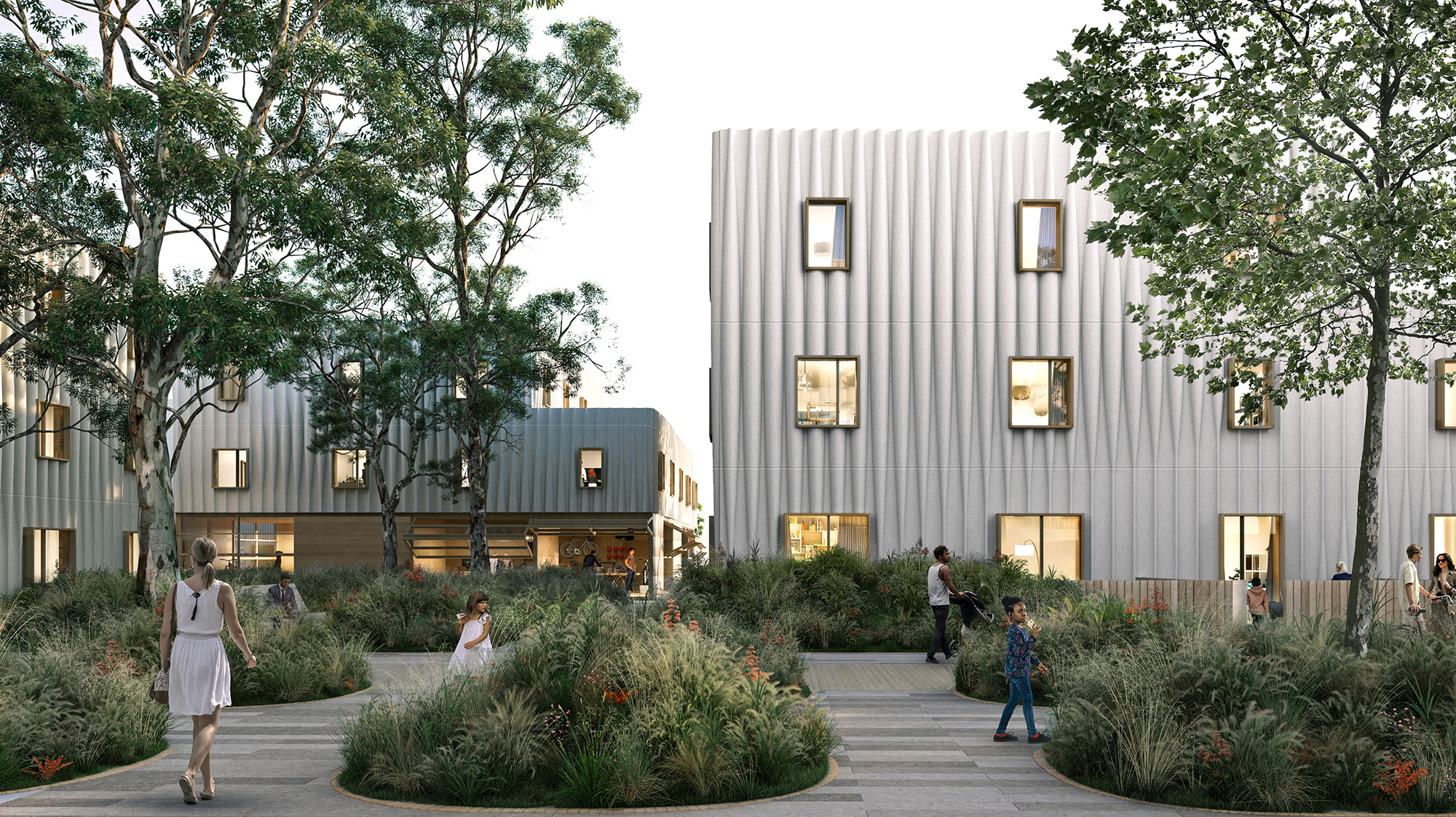
The façade presented an additional challenge for the team, as building façades often account for a significant portion of embodied carbon and can take months to install. Rather than take a traditional route, The Phoenix team turned to an innovative, sustainable biomaterial called MycoComposite to form the core of the façade.
Created by Ecovative, MycoComposite is a combination of mycelium—the living root structure of mushrooms—and shredded hemp stalks. Ecovative grows the material in just seven days, which absorbs more carbon than it emits, before forming the core to a fiber-reinforced-polymer shell. The Phoenix team used this to create 36-foot-long panels that act as the building’s carbon-negative façade.
These MycoComposite panels offer five performance benefits: structural, waterproofing, acoustic dampening, thermal insulation, and fire resistance. According to MBH, they can be used as-is with today’s building codes and construction methods.
The use of MycoComposite for The Phoenix marks the first use of the biomaterial in a commercial or residential building. Its use will shave another five months off the construction schedule as well, according to MBH.
Related Stories
Affordable Housing | Feb 22, 2023
Passive House, sustainability standards meet multifamily development
These multifamily developments are not only Passive House (PHIUS) certified, but affordable for tenants.
Affordable Housing | Feb 15, 2023
3 multifamily projects dedicated to 100% living affordability
BD+C editors collected over 20 multifamily projects with a focus on affordable housing. These three developments took it to the extreme.
Affordable Housing | Feb 15, 2023
2023 affordable housing roundup: 20+ multifamily projects
In our latest call for entries, Building Design+Construction collected over 20 multifamily projects with a focus on affordable housing. Here is a comprehensive list of all projects in alphabetical order.