The embodied carbon (EC) intensity in core and shell industrial buildings in the U.S. averages 23.0 kilograms per sf, according to a recent analysis of 26 whole building life-cycle assessments. That means a 300,000-sf warehouse would emit 6,890 megatons of carbon over its lifespan, or the equivalent of the carbon emitted by 1,530 gas-powered cars driven for one year.
Those sobering estimates come from a new benchmark study, “Embodied Carbon U.S. Industrial Real Estate,” which advocates for the measuring and reducing of EC in core and shell industrial buildings, one of the more vibrant commercial construction sectors.
The report was produced by BranchPattern, a Kansas City-based building consultancy dedicated to creating a better built environment. BranchPattern’s study partners for this report include Prologis, Brookfield Properties, IDI Logistics, Bridge Industrial, and Affinius Capital.
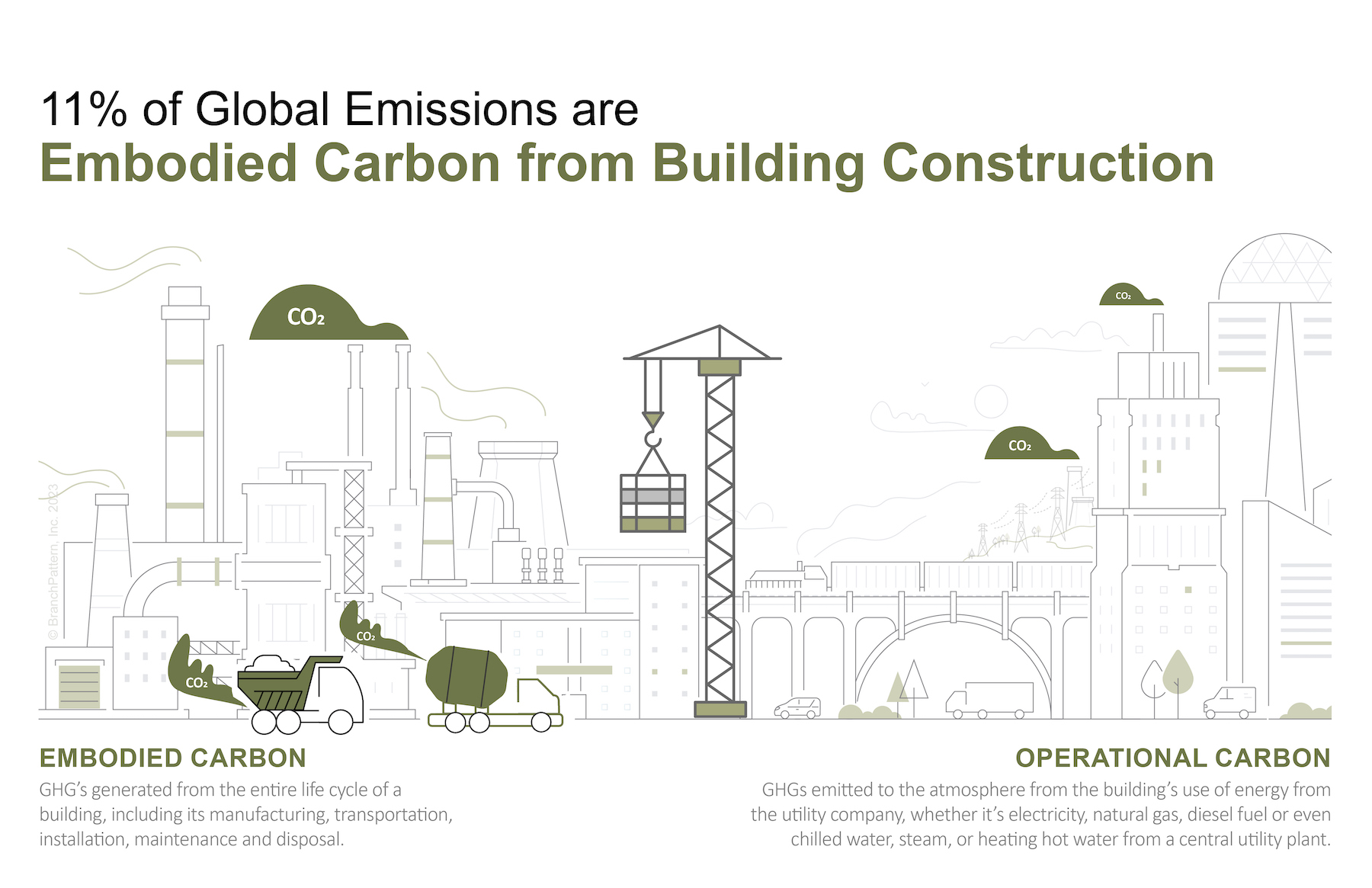
“We are at a pivotal moment for owners and developers of real estate to look beyond the greenhouse gasses emitted during building operations,” says Chris Brown, IDI Logistics’ Solar Development and ESG Director. “Working with industry peers, key partners, and suppliers to create pathways to lower carbon materials, design and construction techniques is an integral part of reducing the impact of buildings have in climate change.”
Building operations and building construction account for 28% and 11%, respectively, of global greenhouse gas emissions, according to the International Energy Agency. As buildings have become more energy efficient, operational carbon has been reduced. Therefore, addressing EC emissions “will become increasingly critical to meet climate goals,” states BranchPattern’s report, especially given that the global building area for industrial typologies is projected to double by 2050.
Right now, most of the available EC data are derived from lifecycle assessments of multifamily and office buildings. But based on conservative assumptions, EC is projected to account for 17.4% of a typical industrial building’s total emissions over 60 years. The report calls for greater access to EC measurement tools and comparative data that can help the industrial sector making informed design and construction decisions.

Stakeholders within an industrial building project have varying responsibilities and financial interests in reducing EC in their buildings. The developer, for example, makes decisions about building materials and design. The tenant, on the other hand, might participate in improvements that include MEP systems and interior finishes.
A small but telling sample
In 2022, BranchPattern conducted 46 lifecycle assessments, of which 26 for nine separate real estate developers or owners in six geographic regions of the U.S. are included in its report. The analyses were confined to Class A core and shell industrial warehouses of similar scope. The reference period for the lifetimes of the buildings was 60 years.
BranchPattern compared its EC intensity finding with a 2017 Carbon Benchmark Study of two buildings whose average EC intensity was 20.2 kg per sf.
The report concedes that its own sample isn’t large enough from which to draw definitive conclusions. “A larger, more robust dataset is required to determine regional variation with statistical significance,” the report states. That being said, BranchPattern’s study shows “a strong, positive, linear correlation” between a building’s size and its EC emissions.
The report finds that, on average, 55% of an industrial warehouse’s EC comes from its structure and enclosure, such as slab-on-grade, exterior walls, framing, and roofdeck. Consequently, an optimal EC reduction strategy addresses emissions from building materials like concrete and steel, which alone account for 11% and 10%, respectively, of global greenhouse gas emissions. For example, cement accounts for about 80% of the carbon emissions from a traditional concrete mix. Switching that mix from 100% ordinary Portland Cement to 50% fly ash/slag cement could reduce the mix’s carbon footprint by approximately 40%.
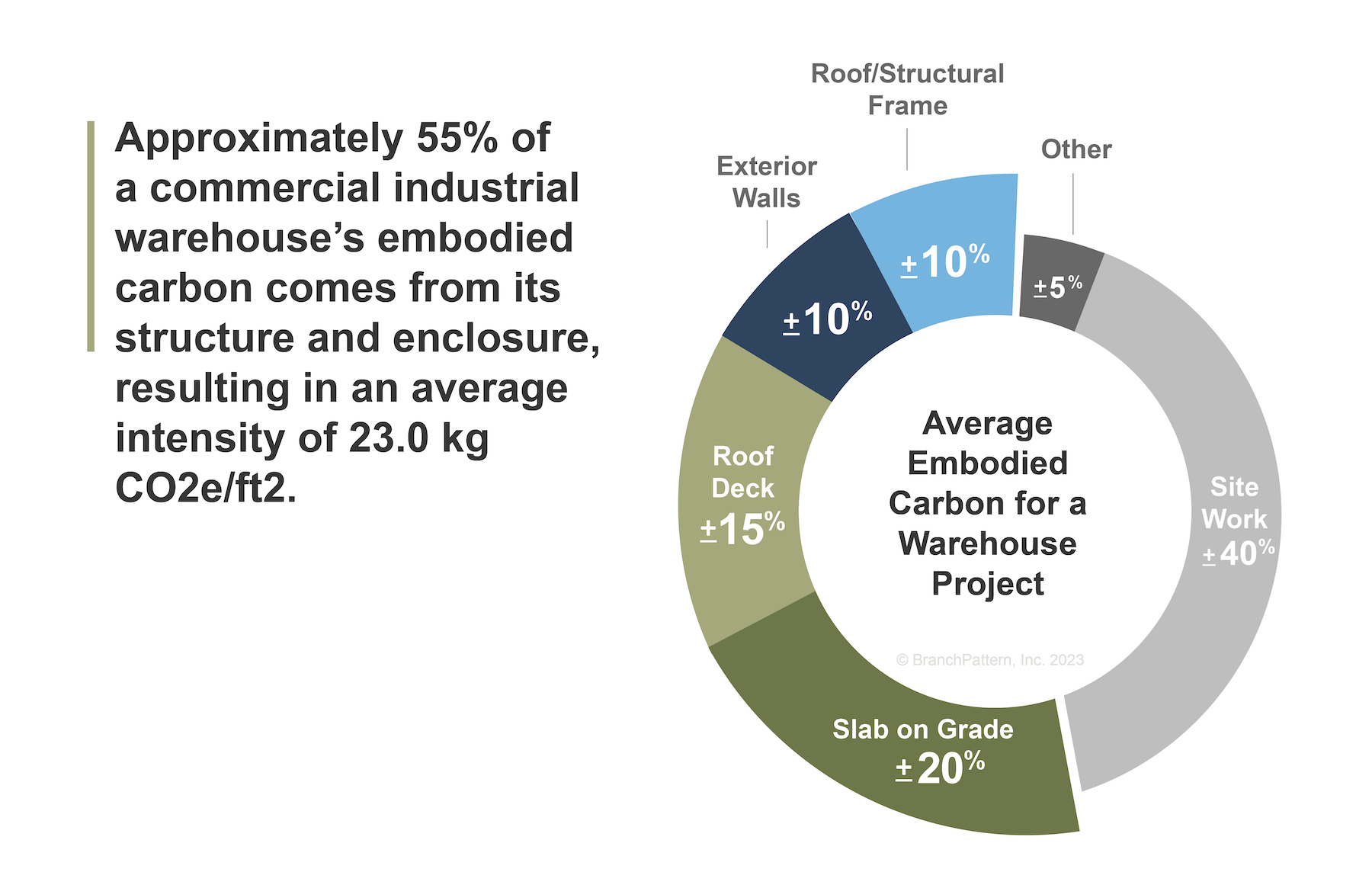
Buildings might also be designed to reduce their overall concrete volume via alternate wall assemblies or insulated metal panels. BranchPattern’s report estimates that substituting mass timber for steel or concrete assemblies would reduce the carbon footprint from the building’s structure/enclosure by 50%. (Affinius Capital recently completed a 161,200-sf Class A warehouse with mass timber, resulting in a 60% reduction in EC compared to a concrete build.) Even using Electric Arc Furnace-produced steel instead of basic oxygen furnace-produced steel cuts EC emissions by 40% to 60%.
Electric Arc Furnace steel is more likely to have a higher recycled content. Recycled materials in general typically have lower EC than virgin materials. However, the report observes that conventional demolition is still cheaper than recovering materials, especially wood. “A building designed for disassembly may have greater residual value, as the integrity of more materials is preserved.”
A call to action

The Paris Climate Accords have set a goal of reducing greenhouse gas emissions 40% by 2030, compared to 1990 emissions. To achieve that goal, “we must now focus on embodied carbon,” the BranchPattern report states. That will require transparent and clear carbon accounting methods that support stakeholder engagement. “To reduce, we must measure,” asserts the report.
Government funding and policy changes are increasing the development and implementation of low-carbon construction solutions. Green building certification programs “will continue to play a significant role mainstreaming embodied carbon knowledge within various building sectors,” the report predicts. The availability of lower-carbon materials will increase and be cost competitive. Engineering solutions in areas like carbon capture, utilization and storage will advance.
“Embodied carbon related emission reductions are possible, necessary, and promising,” the report concludes.
Related Stories
| Aug 11, 2010
New York Mayor Bloomberg opens nation's first multi-story green industrial facility and announces new green manufacturing plant at Brooklyn Navy Yard
Mayor Michael R. Bloomberg, Deputy Mayor for Economic Development Robert C. Lieber, and Brooklyn Navy Yard Development Corporation Chairman Alan Fishman and President Andrew H. Kimball today opened the Perry Avenue Building, the nation's first multi-story green industrial facility at the Brooklyn Navy Yard. Mayor Bloomberg also announced the creation of Duggal Greenhouse, a 60,000-square-foot LEED Platinum certified facility.
| Aug 11, 2010
ASHRAE introduces building energy label prototype
Most of us know the fuel efficiency of our cars, but what about our buildings? ASHRAE is working to change that, moving one step closer today to introducing its building energy labeling program with release of a prototype label at its 2009 Annual Conference in Louisville, Ky.
| Aug 11, 2010
USGBC considering LEED for Data Centers program
In a blog post this morning on Earth2Tech, Justin Moresco writes that the U.S. Green Building Council is giving strong consideration to developing a version of its LEED green building rating system for data centers.
| Aug 11, 2010
10 tips for mitigating influenza in buildings
Adopting simple, common-sense measures and proper maintenance protocols can help mitigate the spread of influenza in buildings. In addition, there are system upgrades that can be performed to further mitigate risks. Trane Commercial Systems offers 10 tips to consider during the cold and flu season.
| Aug 11, 2010
Jacobs, Holder Construction top BD+C's ranking of the nation's 50 largest industrial building contractors
A ranking of the Top 50 Industrial Contractors based on Building Design+Construction's 2009 Giants 300 survey. For more Giants 300 rankings, visit http://www.BDCnetwork.com/Giants
| Aug 11, 2010
AECOM, Arup, Gensler most active in commercial building design, according to BD+C's Giants 300 report
A ranking of the Top 100 Commercial Design Firms based on Building Design+Construction's 2009 Giants 300 survey. For more Giants 300 rankings, visit http://www.BDCnetwork.com/Giants
| Aug 11, 2010
Turner Building Cost Index dips nearly 4% in second quarter 2009
Turner Construction Company announced that the second quarter 2009 Turner Building Cost Index, which measures nonresidential building construction costs in the U.S., has decreased 3.35% from the first quarter 2009 and is 8.92% lower than its peak in the second quarter of 2008. The Turner Building Cost Index number for second quarter 2009 is 837.
| Aug 11, 2010
AGC unveils comprehensive plan to revive the construction industry
The Associated General Contractors of America unveiled a new plan today designed to revive the nation’s construction industry. The plan, “Build Now for the Future: A Blueprint for Economic Growth,” is designed to reverse predictions that construction activity will continue to shrink through 2010, crippling broader economic growth.