Urban, market-rate housing that lower-income workers can actually afford is one of our country’s biggest needs. For multifamily designers, this challenge presents several opportunities for creating housing that workers such as entry-level teachers can afford on their salaries.
Three promising strategies are modular construction, adaptive reuse, and micro-units.
Multifamily Modular Construction Criteria for ROI
This is one of the most exciting evolutions in housing. We have studied modular construction and prefabricated panels/assemblies for more than 20 years, integrating them into multifamily projects whenever viable. Our three criteria for assessing modular’s ROI viability for a project:
- Design Flexibility
- Project Location
- Scale
1. Design Flexibility
One misconception about modular construction is that design choices are made strictly by factory-affiliated designers so that the individual modules will fit on a flatbed for truck delivery. Within that restriction, we’ve found surprising latitude working with modular manufacturers to customize the design to fit the local context and job-site configuration. Modular manufacturers are generally open to design input on floorplans, materials, appliances, and more.
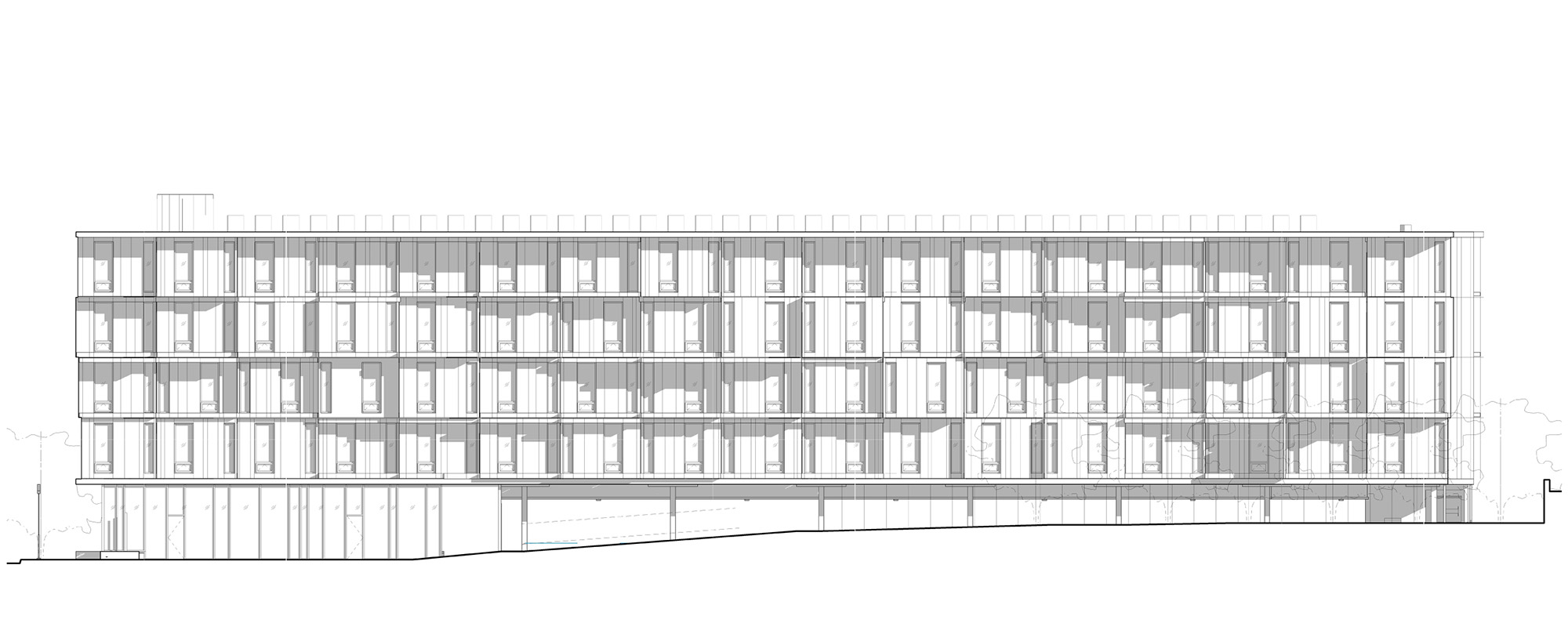
While initial design conversations often discuss downplaying and obscuring the process, we prefer to lean into modular’s building-block bones. As Lego fans, like many AEC professionals, we celebrate the stacked-and-stitched approach to these projects. Realization can include staggering certain modules to accentuate the individual pieces. Further, prefabricated exterior panels and assemblies elevate the assembly-line panache.
2. Project Location
The site has enormous impact on a project’s suitability for modular construction. So that delivery costs don’t negate modular’s advantages over traditional stick-built construction, the site should ideally be within a day’s drive of a suitable factory—generally 400 miles or less, pending topography, population density/traffic, weather, and other variables. Further, rectangular parcels, even narrow infill ones, are well suited to modular construction.
3. Scale
Size of the project is the third determining factor. Under present modular manufacturing capabilities, we feel that 350 apartment units is the upper limit for factory-built modules to be delivered on a financing-viable timeline. Manufacturing capacity should increase in the near future as capital investment accelerates both the number and plant sizes of factories throughout the country. Several states now offer economic stimulus programs that encourage modular manufacturing and project development.
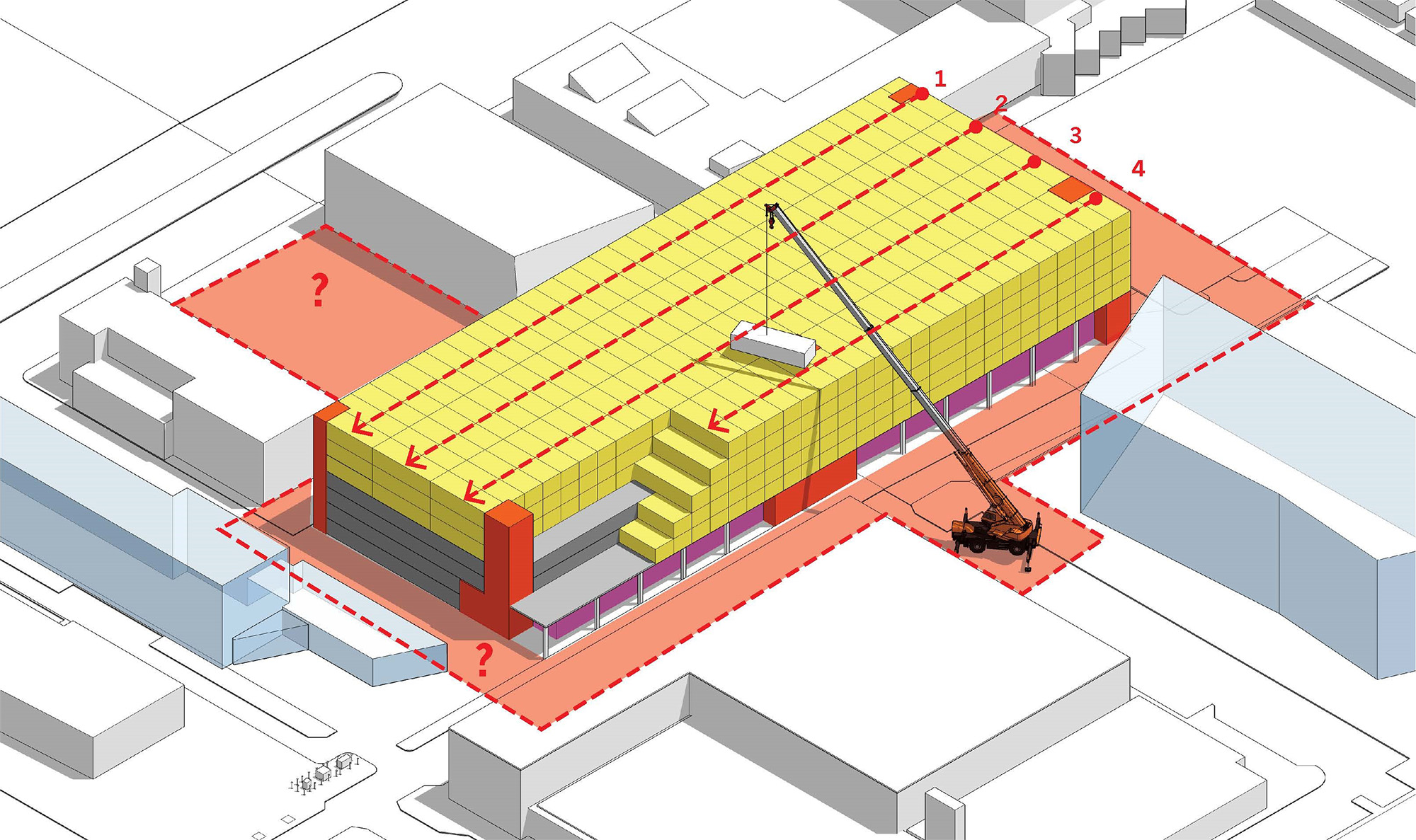
Housing Shortage Solutions with Modular and Prefab
We see modular as an emerging solution for the housing shortage in three primary areas:
Affordable Housing
Since these projects take considerably longer to navigate the layers of government regulations than market-rate projects, modular can save build time for smaller affordable housing projects. As modular manufacturing competition and capacities increase, build costs could conceivably be more advantageous than budgets for stick-built projects.
Missing Middle
Modular construction can accelerate development of market-responsive apartments. Compressing project timelines and saving costs will motivate developers to profitably do projects that rent to tenants earning entry-level wages.
Student Housing
Colleges often have fewer entitlement restrictions than market-rate housing. Modular construction offers college administrators more options for efficiently expanding student housing. On-campus housing design influences enrollment decisions, and studies show that students who live on campus have higher GPAs and better mental health.
Modular Construction Advantages and Disadvantages
The modular construction process has several advantages:
Time
Traditionally, construction financing drives the project timeline. When all stakeholders are organized and aligned, modular can save significant time compared to traditional construction—we currently estimate about 30% faster. Inspections are expedited. Modular manufacturers build the pods to comply with relevant codes, and regular assembly-line inspections ensure compliance.
Scheduling and coordination among all stakeholders are crucial to project success. The ultimate goal is to schedule module delivery to begin as soon as the site is ready; storage costs for completed modules can undermine modular’s advantages. Preliminaries—where a modular-literate architect can be invaluable—include finalizing the design, working with the factory to include materials, and selecting FF&E readily available in the current supply chain.
Construction
Site construction is dramatically simplified. Once the pods arrive at the build-ready site, the modules are placed and connected. Change orders and subcontractors are minimized. Further, module assembly requires smaller crews. This is a huge advantage under the current labor shortage, and smaller crews equate to fewer workers’ comp claims. We’ve found that working with a builder who’s previously done modular projects eliminates what can be a considerable learning curve.
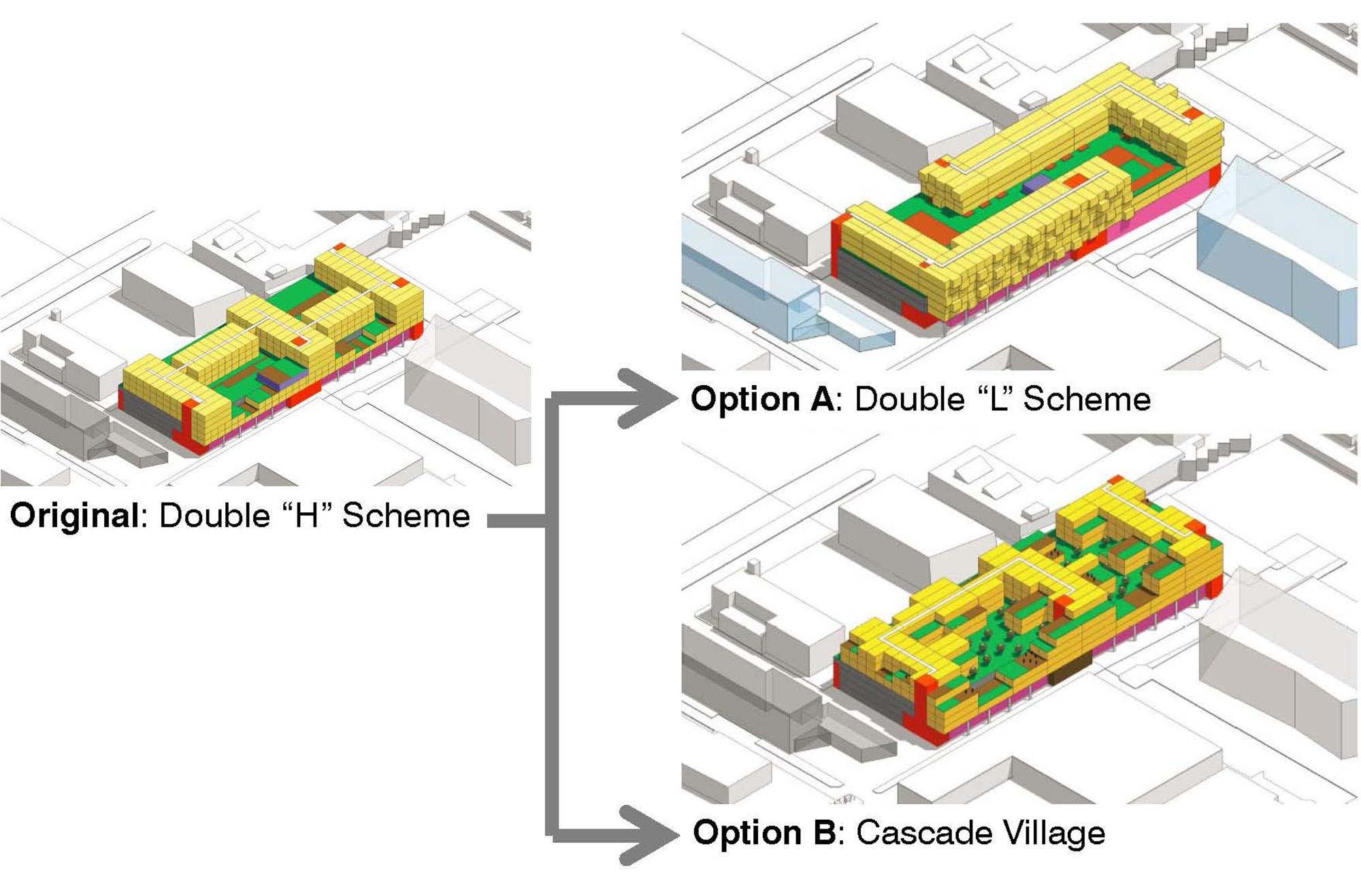
Quality
Automated manufacturing minimizes human error. Quality control is also higher in a factory than on a job site. Even better, each module is wrapped in insulation. This improves thermal performance and sound absorption over traditional construction. One-inch airspace between assembled modules further elevates R-value and increases sound isolation.
Sustainability
Because factory assembly is tightly controlled, materials can be accurately ordered for each project. This minimizes build waste to about 3% for what amounts to approximately 70% of the project’s overall construction. Landfill waste is significantly reduced.
There is one main challenge:
Financing
Financing must be front loaded. In the pro forma, developers must account for large spikes in deposits to the modular manufacturer for ordering materials, finishes, and appliances as a precursor to setting up the assembly line. Lenders can be an obstacle here, as most are accustomed to smaller deposits spread out during the process for stick-built construction. Once banks understand and embrace modular’s shorter loan durations, they will be more enthusiastic. In effect, the overall project timeline is recalibrated, yet is still driven by the construction loan.
Adaptive Reuse, Micro-Units for Residential Conversions
With demand for commercial office space plummeting since the pandemic, landlords are desperate to increase occupancy of existing—and sometimes brand-new—buildings. Residential conversions are a popular topic among politicians. We assess conversion viability on three factors:
- Floor plate
- Condition of the existing mechanical system
- Building envelope
Rectangular floor plates lend themselves to apartment configuration. Odd-shaped buildings do not convert into expected apartment configurations. However, a few oddly shaped spaces can be more viable as community amenities.
In some buildings, updating and upgrading MEP systems for beyond workday demands can be cost-prohibitive. Similarly, the existing envelope can increase MEP load. Lack of operable windows is one example common in buildings from the 1970s.
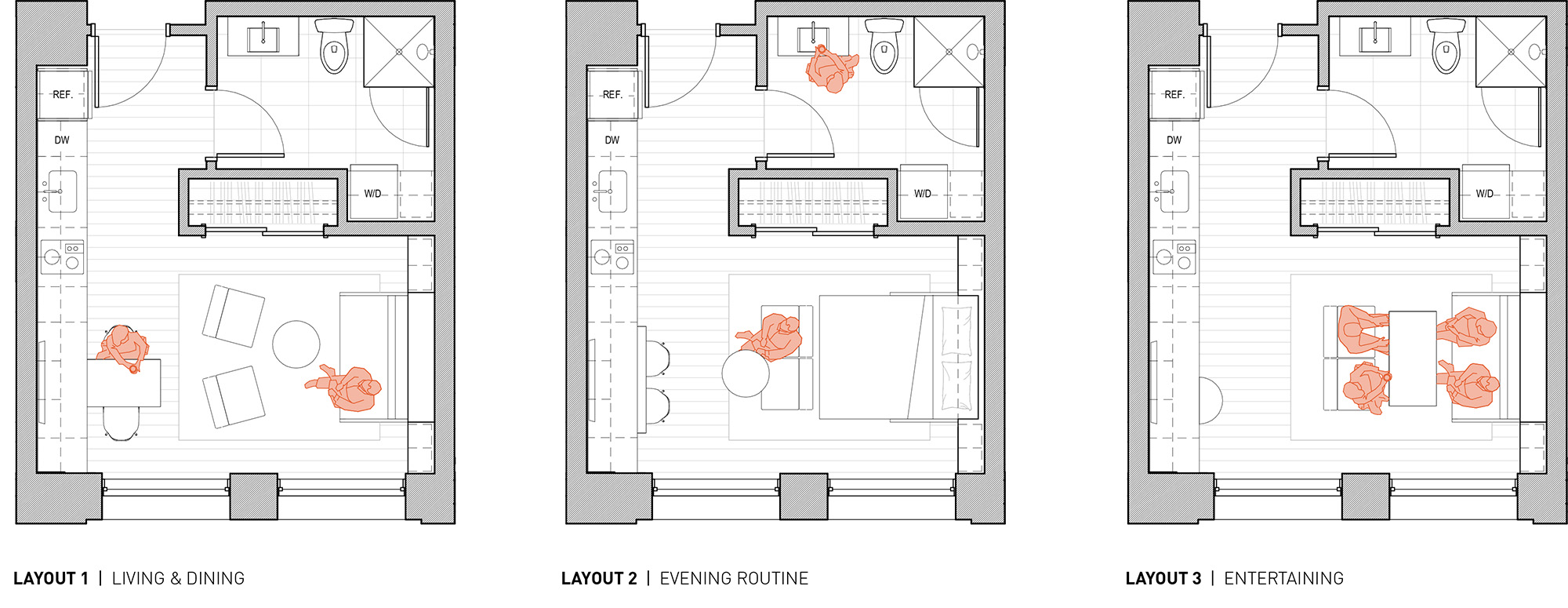
A recent project that combines adaptive reuse of an office building is Midland Lofts in downtown Kansas City. Developer Cordish Company challenged us to transform a long-vacant 1926 Historic Register-listed building whose previous tenants include AMC Theater’s corporate offices into attainable apartments. Cordish identified a local need for monthly rents beginning at about $700 and will select a deserving city employee to receive a year’s free rent at Midland Lofts.
Our initial design fit 117 apartments. Upon further review, we squeezed in 139 units, with studios ranging between about 320 and 470 sf. Odd-shaped niches house amenity spaces, such as a music room/studio and yoga area. Additional communal amenities of a commercial kitchen and co-working lounge supplement the micro-unit apartments. Design inspiration came from the historic Midland Theater, still thriving in the non-tower portion of the building.
Multifamily’s future is encouraging. Micro-unit apartments and modular construction are two design solutions aimed at improving affordability and sustainability.
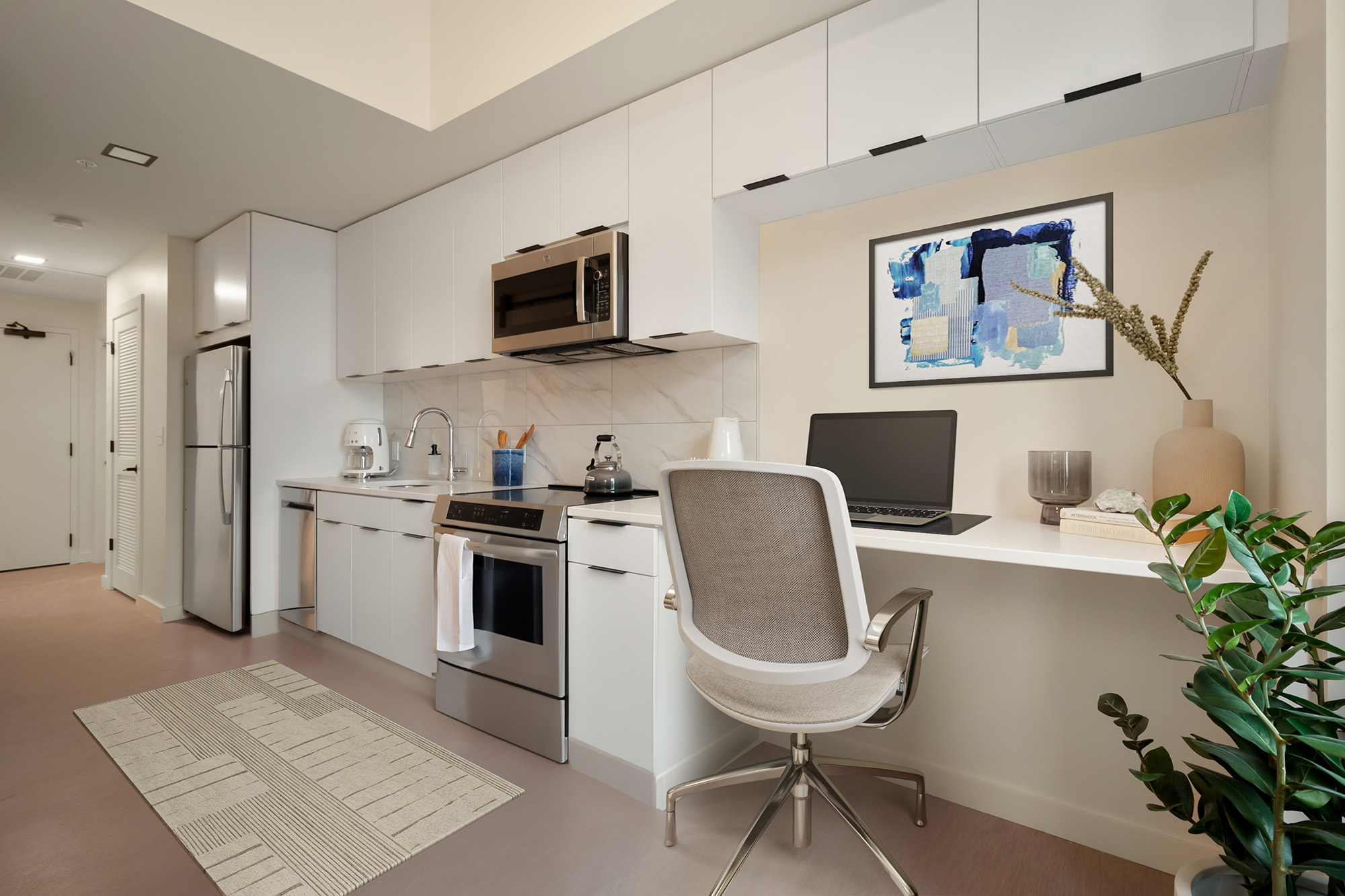
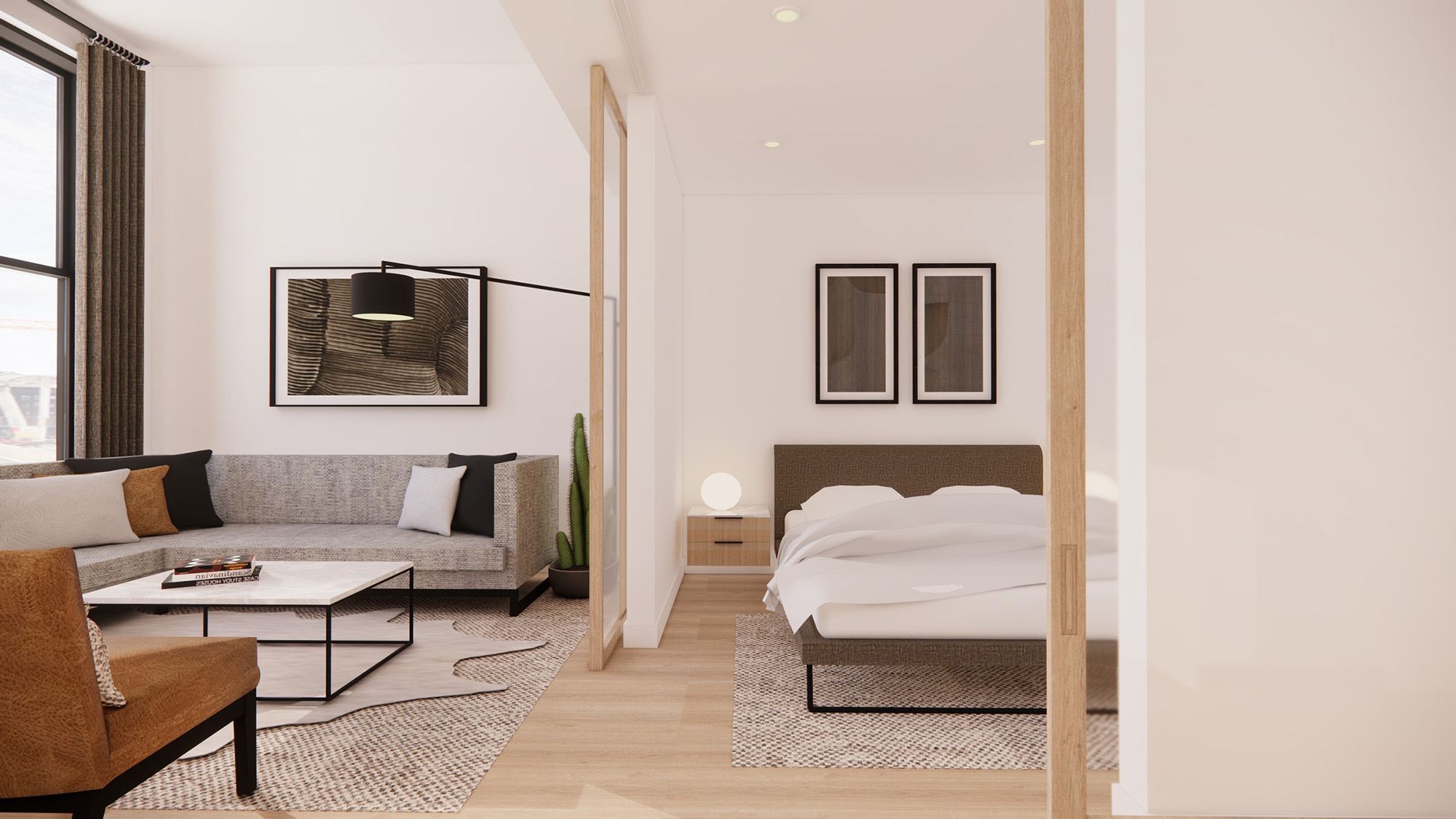
Related Stories
Modular Building | Mar 17, 2020
Danish hospital is constructed from 24 steel frame modules
Onsite construction was completed in two weeks.
Modular Building | Feb 16, 2020
On the West Coast, prefab gains ground for speedier construction
Gensler has been working with component supplier Clark Pacific on several projects.
Modular Building | Nov 18, 2019
A modular solution to help reduce homelessness
DOME is a Perkins and Will-designed prototype whose goal is to provide bridge housing to the unsheltered.
AEC Innovators | Aug 13, 2019
Stacking the deck: Marriott International embraces modular construction
The hotel giant has more than 50 projects in the works that incorporate prefab guestrooms or bathrooms.
Modular Building | Jul 3, 2019
World’s tallest modular building rises in Singapore
The state has been pushing for improvements in construction management.
Modular Building | May 13, 2019
This Marriott is poised to take over the title as the world’s tallest modular hotel
Danny Forster & Architecture designed the building.
Sponsored | Modular Building | Jan 22, 2019
Folsom Hotel opens five months early using modular construction
Early check in? With modular construction the answer is yes!
Modular Building | Oct 31, 2018
Europe’s citizenM is trying to crack into the U.S. hotel market with steel-framed modular construction
Projects in several cities are in various stages of development.
Modular Building | Oct 12, 2018
DeSimone Consulting Engineers designs the tallest modular hotel in the United States
The hotel was originally designed as a cast-in-place concrete structure.
Modular Building | Sep 25, 2018
Amazon invests in a prefab module supplier
Los Angeles-based Plant Prefab targets single- and multifamily construction.