The phoenix: a mythological bird that symbolizes resurrection, rebirth, and life after death. Demolished in 1989, The Phoenix Ironworks Steel Factory left a five-acre hole in West Oakland, Calif. After sitting vacant for nearly three decades, the site will soon become utilized again as The Phoenix rises from the ashes—this time in the form of 316 affordable housing units.
In a collaboration between MBH Architects, modular construction company Factory_OS, technology provider Autodesk, bio-materials company Ecovative, building envelope consultant Heintges, and fabricator Kreysler & Associates, The Phoenix aims to be a revolutionary development made possible through groundbreaking biomaterials, innovative building methods, and Autodesk’s Design and Make Platform, which connected these teams and their data through cloud-based workflows and provided AI-powered insights.
AI Brings Affordable Housing Project to Life
In the case of The Phoenix, AI played a heavy role in optimizing the design of the affordable housing development.
The team used Autodesk Forma in early-stage design to “rapidly explore a wide range of design options that would simultaneously meet the project’s goals for cost, carbon, and livability,” according to David Benjamin, Director, AEC Industry Futures at Autodesk.
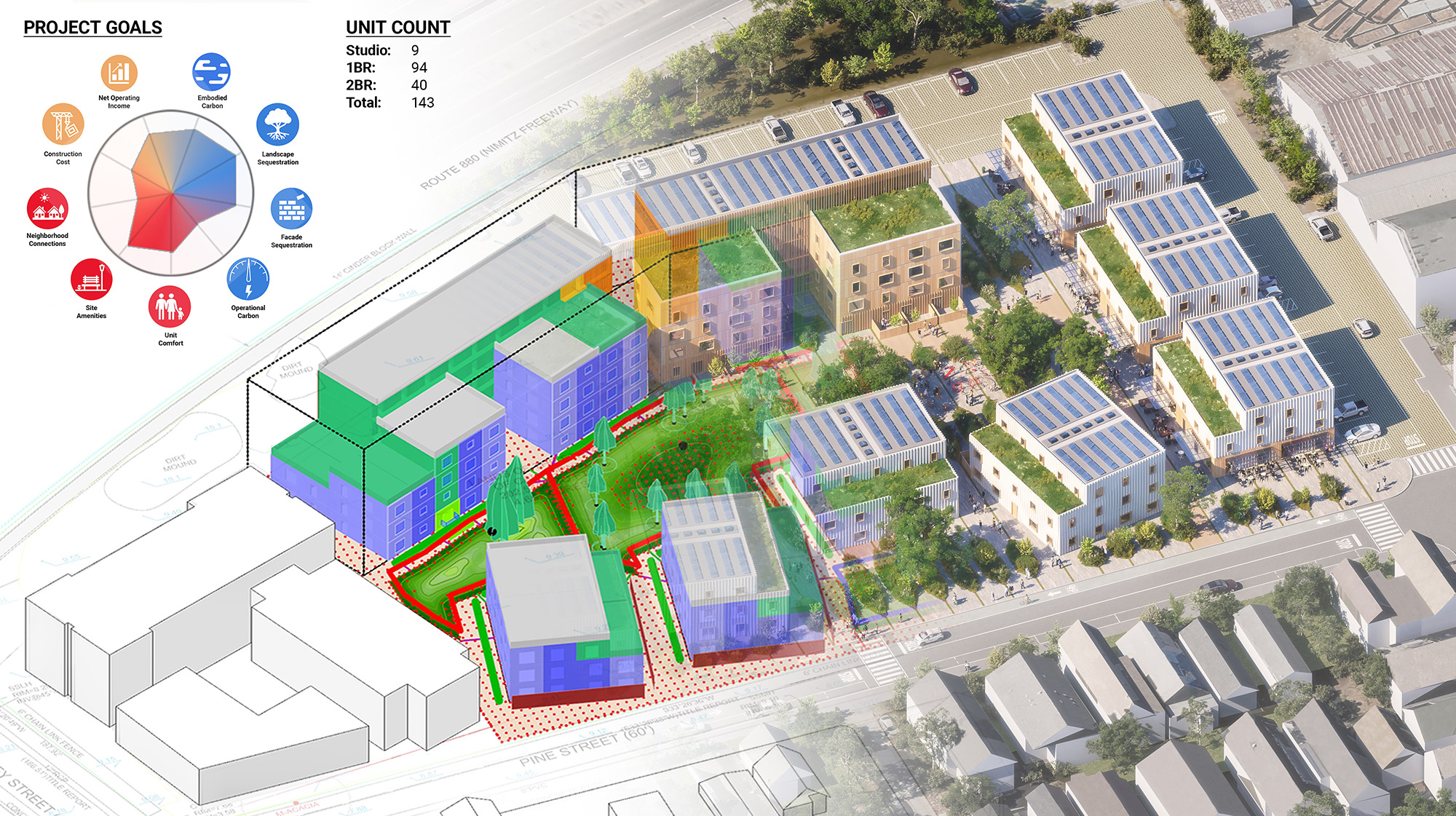
These capabilities allowed MBH to adjust and analyze different multifamily designs—such as adding buildings, or moving around structures and greenspaces—to find the most optimal layout.
One analysis the project team did was to test how different building configurations were affected by noise from nearby highway traffic. With Autodesk Forma’s AI-powered tool, Rapid Noise Analysis, MBH Architects could optimize the final placement of structures on the building site to minimize noise. By using this technology MBH could explore the range of options and was able to complete an initial design package in just six hours—compared to the typical timeframe of two weeks.
“Time saving is probably the biggest benefit of [AI] tools, which enable us to ensure faster delivery of much-needed housing solutions,” says Ryan McNulty, Principal, Architect, MBH Architects.
Autodesk Forma was also used to measure goals for operational and embodied carbon, cost, and livability. The tool helped the team iterate on various designs like relocating playgrounds or shifting buildings to land on a final design that met the needs of the developer, the community, and stakeholders.
![]() | ![]() |
Through this process, The Phoenix is projected to be completed in half the time, cost, and carbon footprint of a typical multifamily housing project in the Bay Area, which made the project eligible for state incentives, according to McNulty. While AI and cloud-based workflows supplied ample time-saving benefits on the front end, volumetric modular construction will present additional cost-effective opportunities once on-site construction begins.
Modular Construction with Innovative Biomaterials
Manufactured by Factory_OS, the modular units of The Phoenix can be assembled in just 10 days, according to MBH. Though this modular construction method speeds up project delivery, reduces waste, and removes the unpredictability of a traditional construction, it’s not without risk. Efficiently wrapping the modular units to ensure the building becomes weather-tight is “an ongoing design challenge,” says McNulty.
While standardizing window sizes has improved efficiency in building unit fabrication, incorporating prefabricated exterior panels introduces a new layer of complexity. The team is focused on systematizing various elements like windows and FRP panels to enable façade prefabrication.
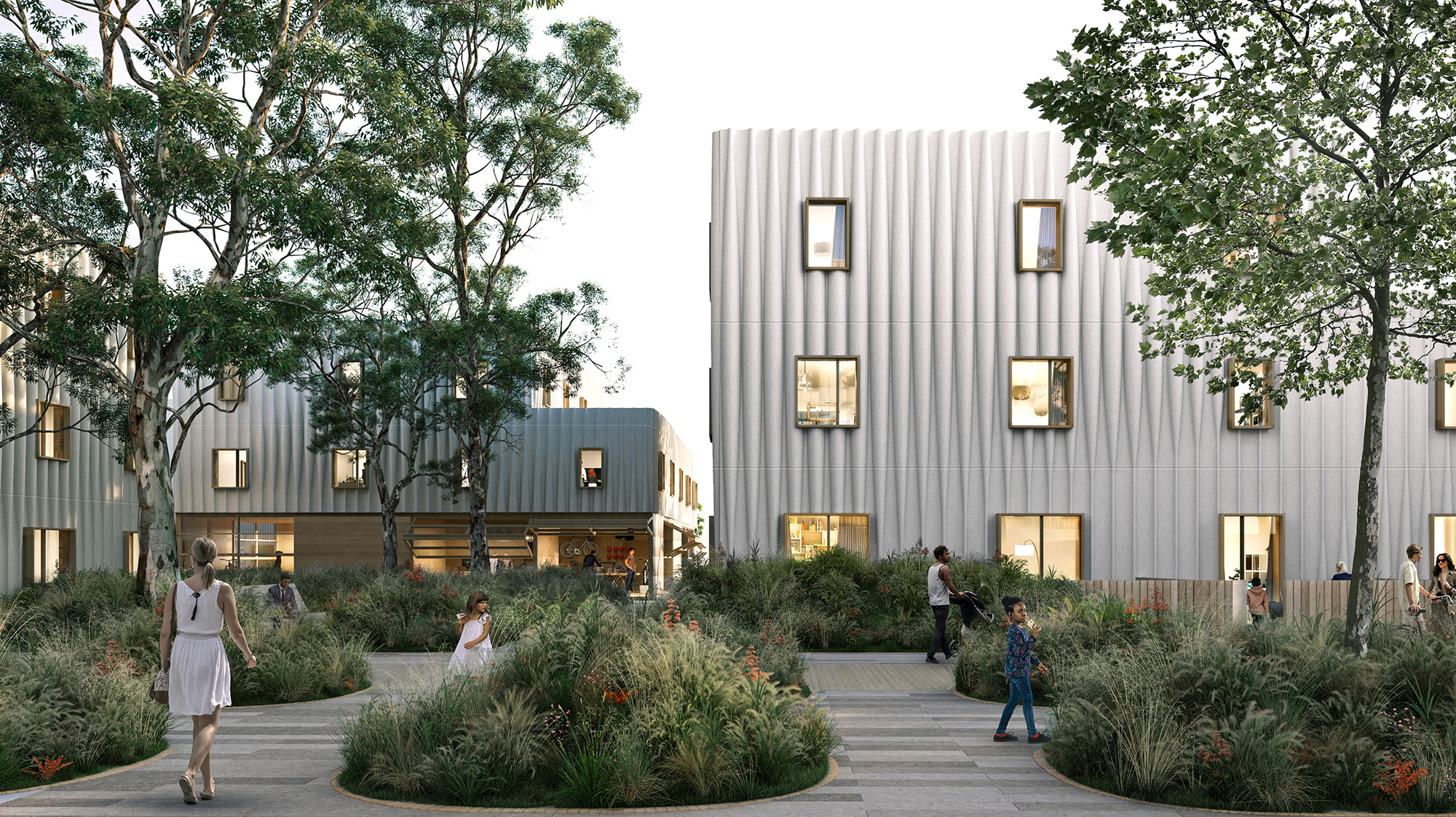
The façade presented an additional challenge for the team, as building façades often account for a significant portion of embodied carbon and can take months to install. Rather than take a traditional route, The Phoenix team turned to an innovative, sustainable biomaterial called MycoComposite to form the core of the façade.
Created by Ecovative, MycoComposite is a combination of mycelium—the living root structure of mushrooms—and shredded hemp stalks. Ecovative grows the material in just seven days, which absorbs more carbon than it emits, before forming the core to a fiber-reinforced-polymer shell. The Phoenix team used this to create 36-foot-long panels that act as the building’s carbon-negative façade.
These MycoComposite panels offer five performance benefits: structural, waterproofing, acoustic dampening, thermal insulation, and fire resistance. According to MBH, they can be used as-is with today’s building codes and construction methods.
The use of MycoComposite for The Phoenix marks the first use of the biomaterial in a commercial or residential building. Its use will shave another five months off the construction schedule as well, according to MBH.
Related Stories
MFPRO+ News | Jul 22, 2024
6 multifamily WAFX 2024 Prize winners
Over 30 projects tackling global challenges such as climate change, public health, and social inequality have been named winners of the World Architecture Festival’s WAFX Awards.
MFPRO+ News | Jul 15, 2024
More permits for ADUs than single-family homes issued in San Diego
Popularity of granny flats growing in California
Vertical Transportation | Jul 12, 2024
Elevator regulations responsible for some of ballooning multifamily costs
Codes and regulations for elevators in the United States are a key factor in inflating costs of multifamily development, argues a guest columnist in the New York Times.
MFPRO+ New Projects | Jul 10, 2024
3 noteworthy multifamily projects for July 2024
These three multifamily projects on our radar include an artist-inspired complex, seven-acres of senior housing, and a budget-conscious rental community.
MFPRO+ News | Jul 8, 2024
Boston receives 304 new market-rate and affordable housing units
The Smith No. 99 in Boston, Mass., is a new 305,000-sf mixed-use apartment community featuring 304 market rate and affordable housing units.
MFPRO+ News | Jun 25, 2024
New York mayor releases multi-year plan to address affordable housing crisis
The plan seeks to create and preserve affordable housing. It will incentivize the inclusion of permanently affordable and rent stabilized housing in new, multi-family construction projects.
MFPRO+ News | Jun 24, 2024
‘Yes in God’s Backyard’ movement could create more affordable housing
The so-called “Yes in God’s Backyard” (YIGBY) movement, where houses of worship convert their properties to housing, could help alleviate the serious housing crisis affecting many communities around the country.
Senior Living Design | Jun 13, 2024
Crystal Pacific Windows bring sunshine to senior living community
Crystal Pacific Window & Door Systems, the West Coast production affiliate of national manufacturer Crystal Window & Door Systems, recently supplied over 400 energy efficient vinyl windows for a new affordable housing community in San Diego, Calif.
Affordable Housing | Jun 12, 2024
Studio Libeskind designs 190 affordable housing apartments for seniors
In Brooklyn, New York, the recently opened Atrium at Sumner offers 132,418 sf of affordable housing for seniors. The $132 million project includes 190 apartments—132 of them available to senior households earning below or at 50% of the area median income and 57 units available to formerly homeless seniors.
Multifamily Housing | Jun 3, 2024
Grassroots groups becoming a force in housing advocacy
A growing movement of grassroots organizing to support new housing construction is having an impact in city halls across the country. Fed up with high housing costs and the commonly hostile reception to new housing proposals, advocacy groups have sprung up in many communities to attend public meetings to speak in support of developments.