Autovol, a modular construction company based in Nampa, Idaho, has taken a comprehensive systems approach to building affordable multifamily housing. The Autovol process, which it calls “automated volumetric modular construction,” uses robotic systems to assemble six-sided modules and equip them with all appliances, fixtures, and MEP systems for shipment to the job site, where they are hoisted and secured into position. From there the utilities are connected and the exterior siding is applied.
The Autovol process differs from panelized modular construction, in which wall, floor, and ceiling panels are built in a plant and assembled on site. The Autovol system breaks down the structure into cubic modules—anywhere from two studio apartments across the hall from each other, to several building blocks forming a two- or three-bedroom unit—to construct a multistory building. The walls can be up to 74 feet in length and 8–10 feet in height.
Autovol opened its 400,000-sf plant in July 2020. It is equipped with 53 ABB six-axis industrial robots, which fully automate the production of the walls, ceilings, and floors that make up the volumetric modules.
The company has four multifamily projects in the works, all in California. All were developed by The Pacific Companies, based in Eagle, Idaho:
- Virginia Street Studios, a $10 million, 301-unit senior affordable all-studio housing community in San Jose, was assembled from 160 modules. It is undergoing final site work and is scheduled to open this spring.
- Santa Maria, a 105-module, 160-unit commercial/residential mixed-unit complex in the city of that name.
- Lemos Pointe at Watson Ranch, a mixed-use affordable community of 186 residences (231 modules) in American Canyon, near Napa.
- MacArthur, 193 senior affordable apartments (136 modules), in Oakland.
The modules for the latter three projects are completed and awaiting shipment to their sites.
ENVISIONING A ROBOTIC CONSTRUCTION PROCESS FOR HOUSING
Autovol co-founder and CEO Rick Murdock, who has been in the manufactured housing industry for 44 years—he co-founded Guerdon Modular Buildings—said he got “hooked on automation” after attending a trade show a few years ago. “I formed this vision of starting a robotically automated modular housing plant that could build a high-quality product while relieving construction workers and tradespeople of the physical stress common to the job.”
Murdock joined forces with Lars Wikholm, owner of Wiksfors Technology, a robotic engineering firm in Sweden, as a consultant. Quite by accident, in 2018, Murdock learned of another robotic engineering firm, House of Design, five miles down the road in Nampa. House of Design, an ABB Robotics system integrator, had recently developed automated roof and floor truss systems for another manufactured housing company.

To design Murdock’s dream factory, House of Design engineers used RobotStudio, ABB’s offline simulation and programming software, to experiment with highly realistic simulations of automation systems, featuring numerous robot models and layout combinations, to reach the optimal design for each robotics line.
The software is able to select and position the line components, such as conveyors and robot tracks, that perform the various manufacturing processes. RobotStudio can identify potential bottlenecks and calculate accurate space requirements and throughput metrics that the system concept would deliver if actually installed on the plant floor. In essence, end-users are able to experiment with system design variations through risk-free trial and error until the ideal system is designed.
“We relied heavily on House of Design to gain an understanding of automation and robotic constraints,” said Curtis Fletcher, Autovol co-founder and CTO.
The resulting robotic construction lines occupy 100,000 sf in the core of the $104 million Autovol plant. The surrounding 300,000 sf is where the walls, floors, and ceilings are assembled into the modules, and where the MEP systems are installed, the walls are painted, and the modules are equipped with appliances and bathroom fixtures.
“All 53 robots were specified in RobotStudio prior to purchase,” said Shane Dittrich, House of Design’s co-owner. “It’s incredibly powerful to have one complete visual representation of the robotic lines, where you can zoom in on, examine, and modify all the key production areas.”
SOFTWARE ENABLES ‘DYNAMIC ROBOTIC AUTOMATION’ OF HOUSING CONSTRUCTION
The brains behind the whole process is House of Design’s Dynamic Robotic Automation custom software and modeling system, which enables Autovol to sequentially build an unlimited number of wall, ceiling, and floor variations on a continuous, uninterrupted production schedule.
The project design starts with Prefab Logic, which is owned by two Autovol co-founders. Prefab Logic gathers all the building codes and other jurisdictional requirements, creates the drawings that break down the structure into modular sections, and develops the BIM model, which House of Design integrates into Autovol’s robotic systems.
“It all starts with software,” said Dittrich. “We are basically making snowflakes, meaning you can have any design you want as long as it is within the established dimensional constraints. At one point we made eight miles’ worth of walls, with 1,500 different wall designs, yet not a single person had to program those walls.”
The instructions “just went through the software and onto the equipment, and the equipment knew exactly what it had to do to build each wall,” said Dittrich. “It’s all automated. That’s why we call it dynamic automation, rather than flexible automation.”
ROBOTIC WALL, FLOOR, AND CEILING PRODUCTION FOR HOUSING
There are two main robotic lines at the plant: one for walls, the other for floors and ceilings. Since each module has end walls, mate walls, and interior walls but only one floor and ceiling, each line can operate continuously, with the throughput for each synchronized so that modules can be assembled as the panels are made.
The wall line’s framing system builds door and window headers, as well as door and window frames. Once these components are completed, they are robotically assembled and placed in the wall as it is extruded.
The framing studs range from 2X4s up to 2X12s. Any combination of windows and doors can be programmed via House of Design’s Dynamic Robotic Automation. “One custom wall design can be made right after another, without any changeover in equipment,” said Brandon Schmidt, House of Design VP of Automation & Robotics.

As a wall is made, robots pick, place, and nail the framing elements to the top and bottom plates, which are placed in the main element extruder that moves the plates forward. Other robots assemble the door and window headers into the corresponding door and window frames, then into the wall as it is extruded down the line.
Once a wall is fully extruded and framed it goes to the sheathing line. Glue is laid down, and the robots pick, place, and fasten layers of OSB or drywall (or both) to one side of the wall. Robots route out electrical boxes and openings for windows, doors, and ventilation—a procedure that requires a great deal of precision to align the openings with the subcomponents.
The wall then moves to an MEP station, where wires, plumbing and electrical boxes, and insulation are manually installed. The panels are shifted to the outer ring of the plant for assembling, finishing, and equipping the modules. The floor and ceiling line operates in much the same way.
At that point, the interior components of the completed modules are secured and the exterior is tightly wrapped in a weather-resistant covering for shipment up to 800 miles from Autovol’s plant.
CALCULATING THE SAVINGS IN DOLLARS AND TIME FROM ROBOTIC MODULAR CONSTRUCTION
Autovol has been in operation for nearly two years, running four 10-hour shifts a week and pumping out about 14 modules a week, or some 700 modules a year. The ultimate goal is 2,000 modules a year.
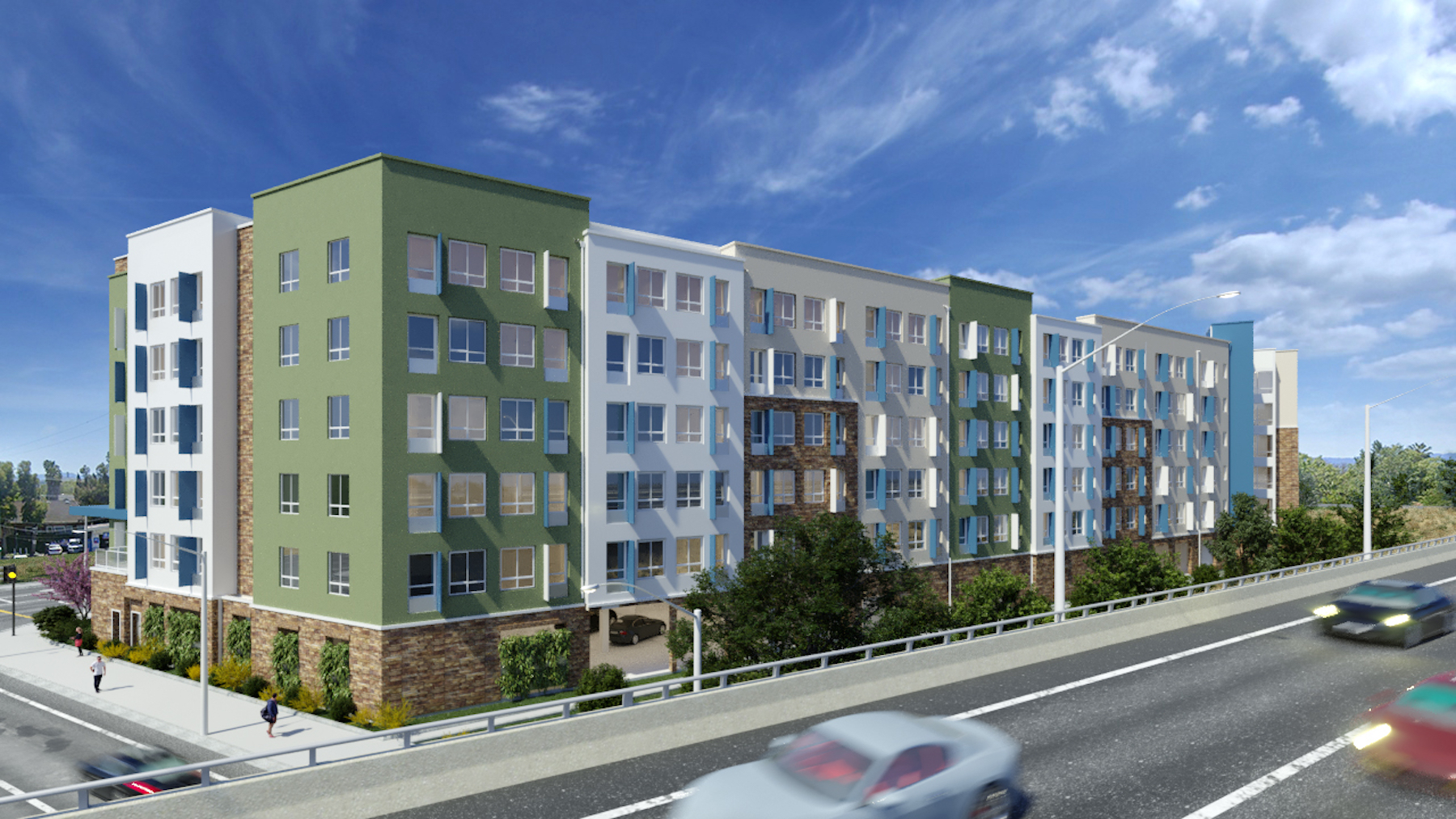
The five-story Virginia Street Studios, in San Jose, was built at a cost of $120/sf; it took about three weeks to erect the 160 modules. Autovol estimates savings of $100/sf, or 20%, off standard building costs in high-cost markets such as the Bay Area, and a time savings of 40% compared to building on site.
Murdock admits that shipping panels might be less costly than shipping completed modules, but “the biggest bang for the buck is to get something delivered on site that is as close to finished as possible.” With panels, “the materials need to be unloaded and organized, and you almost need the same crew on site as if you were stick building.” That makes up for the additional cost of shipping finished modules.
Murdock said his ultimate goal is to expand geographically. “The vision was never for one plant,” he said. “It was for many.”
Related Stories
Affordable Housing | May 17, 2023
Affordable housing advocates push for community-owned homes over investment properties
Panelists participating in a recent webinar hosted by the Urban Institute discussed various actions that could help alleviate the nation’s affordable housing crisis. Among the possible remedies: inclusionary zoning policies, various reforms to increase local affordable housing stock, and fees on new development to offset the impact on public infrastructure.
Sustainability | May 11, 2023
Let's build toward a circular economy
Eric Corey Freed, Director of Sustainability, CannonDesign, discusses the values of well-designed, regenerative buildings.
Design Innovation Report | Apr 27, 2023
BD+C's 2023 Design Innovation Report
Building Design+Construction’s Design Innovation Report presents projects, spaces, and initiatives—and the AEC professionals behind them—that push the boundaries of building design. This year, we feature four novel projects and one building science innovation.
Sustainability | Apr 20, 2023
13 trends, technologies, and strategies to expect in 2023
Biophilic design, microgrids, and decarbonization—these are three of the trends, technologies, and strategies IMEG’s market and service leaders believe are poised to have a growing impact on the built environment.
Design Innovation Report | Apr 19, 2023
Meet The Hithe: A demountable building for transient startups
The Hithe, near London, is designed to be demountable and reusable. The 2,153-sf building provides 12 units of business incubator workspace for startups.
Contractors | Apr 10, 2023
What makes prefabrication work? Factors every construction project should consider
There are many factors requiring careful consideration when determining whether a project is a good fit for prefabrication. JE Dunn’s Brian Burkett breaks down the most important considerations.
Steel Buildings | Apr 6, 2023
2023 AISC Forge Prize winner envisions the gas station of the future
Forge Prize winner LVL (Level) Studio envisions a place where motorists can relax, work, play, shop, or perhaps even get healthcare while their vehicles charge.
Modular Building | Mar 28, 2023
Volumetric Building Companies, a modular manufacturer, designer, and contractor, looks to expand its global presence
The firm wants to break down geographic and regional variances that might impede delivery of its product.
Modular Building | Mar 20, 2023
3 ways prefabrication doubles as a sustainability strategy
Corie Baker, AIA, shares three modular Gresham Smith projects that found sustainability benefits from the use of prefabrication.
Building Tech | Mar 14, 2023
Reaping the benefits of offsite construction, with ICC's Ryan Colker
Ryan Colker, VP of Innovation at the International Code Council, discusses how municipal regulations and inspections are keeping up with the expansion of off-site manufacturing for commercial construction. Colker speaks with BD+C's John Caulfield.